A conveyor system is a common piece of mechanical handling equipment that moves materials from one location to another. These systems are particularly useful in applications involving the transportation of heavy or bulky materials. Comprising an array of critical components, understanding each element's role not only ensures efficient operation but also aids in optimizing overall performance.
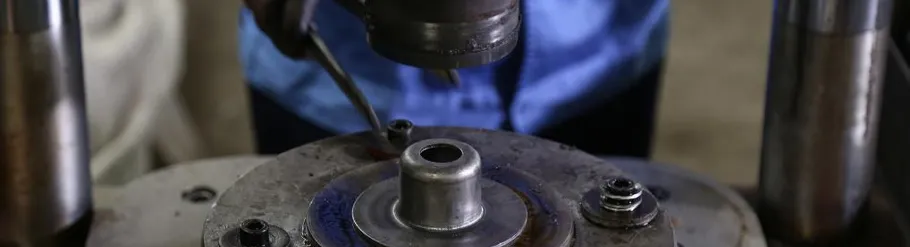
At the heart of any conveyor system lies the conveyor belt itself. Made from a variety of materials such as rubber, plastic, leather, fabric, or metal, the choice of belt material hinges on the specifics of use and the type of material being moved. For instance, a conveyor system tasked with transporting heavy-duty industrial materials might employ a rugged rubber belt, while a system that transports delicate consumer goods might instead utilize a soft fabric belt. The right belt ensures not only the smooth transportation of materials but also contributes to the longevity and maintenance of the entire system.
Supporting the belt is the framework, often referred to as the conveyor structure. This structure needs to be robust, typically crafted from stainless steel, aluminum, or heavy-duty alloy. Its design varies depending on the operational environment and the weight the system needs to support. In industries where hygiene is paramount, such as food processing, stainless steel is preferred due to its corrosion resistance and easy-to-clean surface.
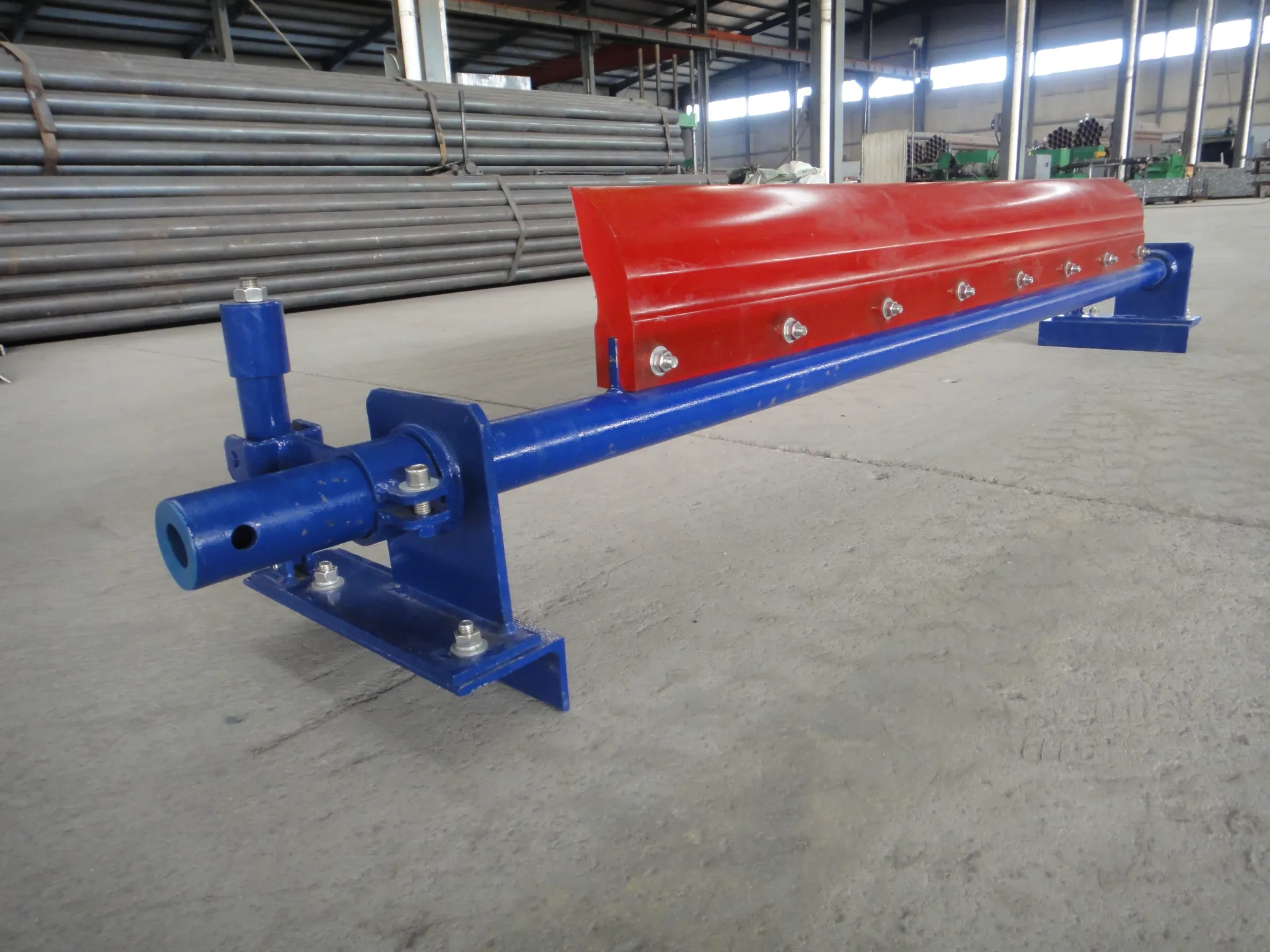
Rollers or drums play a crucial role in facilitating belt movement. Positioned at both ends of the conveyor, these components help guide and control the belt, ensuring it doesn't drift side to side and stays aligned. Constructed from materials like stainless steel or plastic, these rollers must be chosen based on factors such as load weight and system length to prevent operational hiccups like jams or belt misalignment.
components of conveyor system
A driving force is required to move the belt and the materials atop it, which is where the motor and drive mechanism come into play. This component determines the speed and efficiency of the conveyor. The combination of a high-quality motor and a suitable drive system, such as a gear reduction drive or direct drive, ensures that the conveyor system operates with optimal efficiency and energy consumption, directly impacting operational costs and productivity.
Equally important are the control systems. These include sensors, switches, and software that form the brain of the conveyor operation. Modern systems are equipped with programmable logic controllers (PLCs) that allow for automated processes and integration with broader industrial networks. These technological advancements provide real-time data to operators, significantly enhancing the system’s reliability and adaptability.
Safety features are crucial for ensuring the well-being of operators and the longevity of the conveyor system. Emergency stop buttons, guardrails, and warning indicators are typical safety measures that prevent accidents and protect the equipment from damage.
Each component of a conveyor system plays a pivotal role in its overall functionality. By understanding and selecting the right components based on the specific needs and constraints of the application, businesses can create a conveyor system that is not only efficient but also sustainable and cost-effective. As conveyor technology continues to evolve, the trend towards automation and smart integration presents an opportunity for further refinement in performance and safety, reinforcing the importance of choosing high-quality components and implementing advanced control systems.