Rubber lagging pulleys are an essential component in various industrial applications, giving them a crucial role in enhancing the performance and lifespan of conveyor systems. With years of experience in the field of material handling and industrial machinery, I can assure you that the choice of rubber lagging plays a pivotal role in ensuring operational efficiency and reliability.
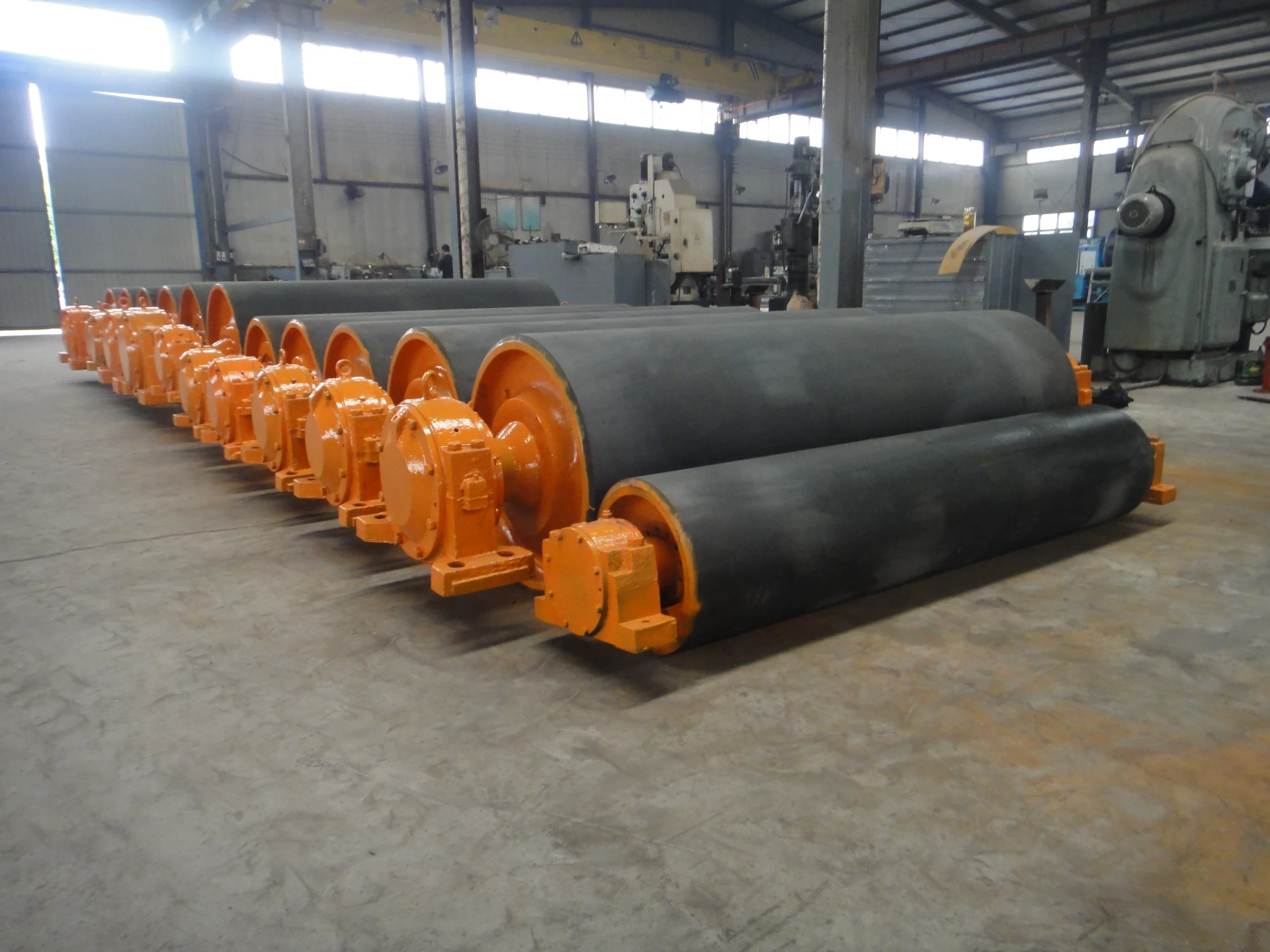
Rubber lagging on pulleys functions primarily to increase the friction between the pulley and the conveyor belt. This friction is vital as it helps in transmitting power from the pulley to the belt, thus ensuring smooth motion and reducing the risk of slippage. The enhanced grip also contributes to reducing wear and tear on the belt itself. For industries such as mining, material transport, and heavy-duty manufacturing, a well-lagged pulley can mean the difference between ongoing maintenance problems and seamless operation.
From a technical standpoint, selecting the proper rubber compound for lagging is critical. The expertise comes into play when understanding the interactions between different rubber compounds and specific operational conditions, such as temperature, load, and environmental exposure. For instance, in environments with high humidity or exposure to oils and chemicals, specially formulated rubber compounds can offer superior resistance and longevity. Through professional assessments and authoritative recommendations, businesses can optimize their conveyor systems for maximum productivity and reduced downtime.
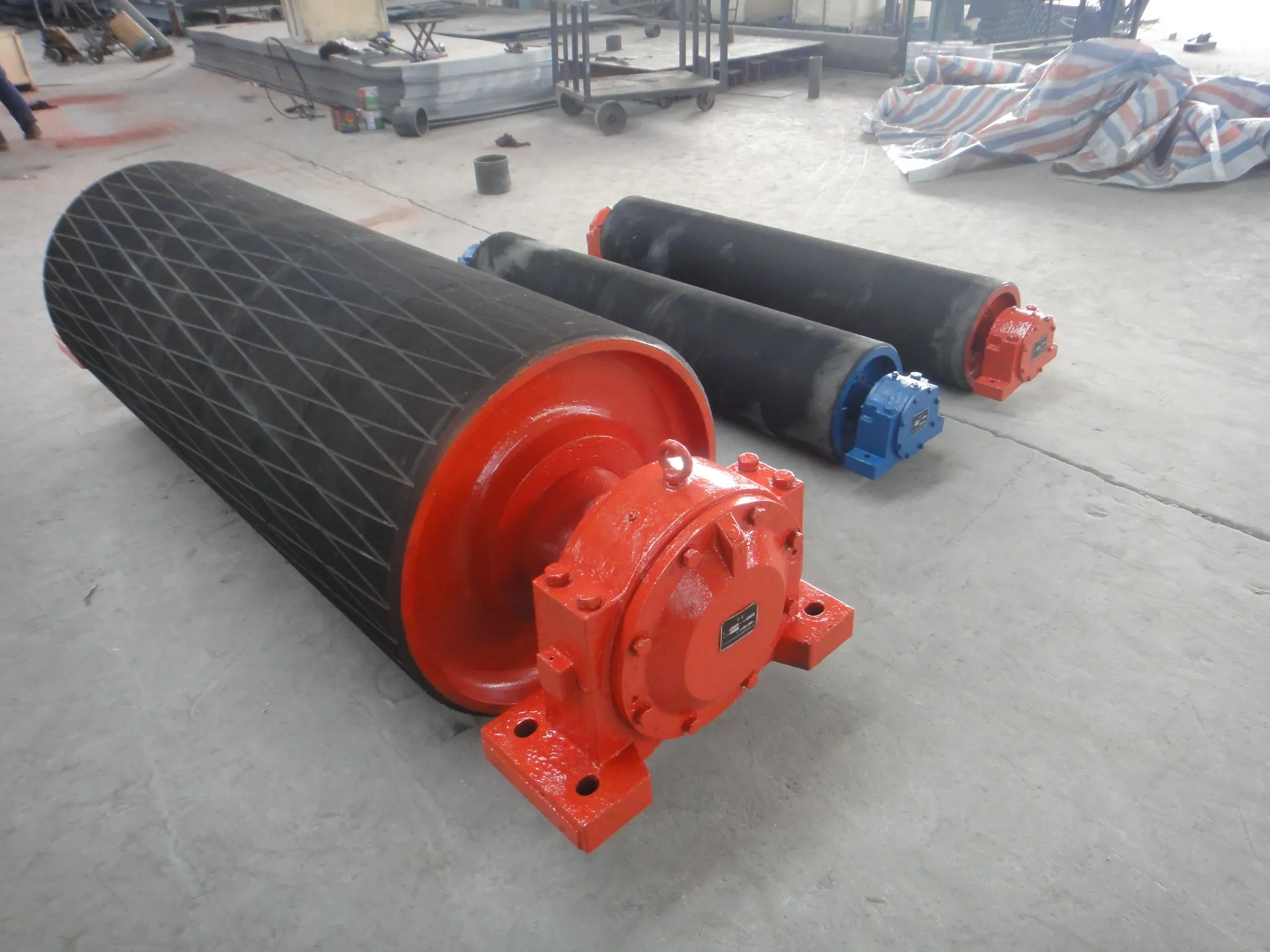
rubber lagging pulley
The authority of a rubber lagging pulley does not just lie in its material composition but also in its design specifications, such as groove patterns. These patterns can either be diamond, herringbone, or plain, each offering distinct advantages depending on the application. Diamond grooves, for example, can provide a self-cleaning action that is particularly beneficial in wet or sticky conditions, enhancing the trustworthiness of the conveyor system under challenging circumstances.
Trustworthiness is further established through the use of rigorous testing and compliance with industrial standards. Manufacturers often subject their rubber lagging to a series of stress tests to ensure resilience under various operational conditions. These tests provide the assurance businesses need, knowing that their pulley systems are equipped with lagging that meets or exceeds industry standards, thereby offering reliability and peace of mind.
In sum, the role of rubber lagging pulleys in industrial applications cannot be overstated. Their contribution to reducing maintenance costs, prolonging belt life, and ensuring operational efficiency makes them an indispensable choice for any business reliant on conveyor systems. By focusing on the right experience, expertise, authoritative standards, and trustworthy practices, companies can maximize their investment in rubber lagging pulleys for improved operational outcomes.