The concept of a picking idler often emerges when discussing conveyor systems, particularly in the context of manufacturing and industrial operations. This mechanical component, seemingly simple, plays a pivotal role in enhancing operational efficiency and ensuring the longevity of conveyor systems. To understand its importance, we must delve deeper into its functionality, benefits, and the expert knowledge required to optimize its use.
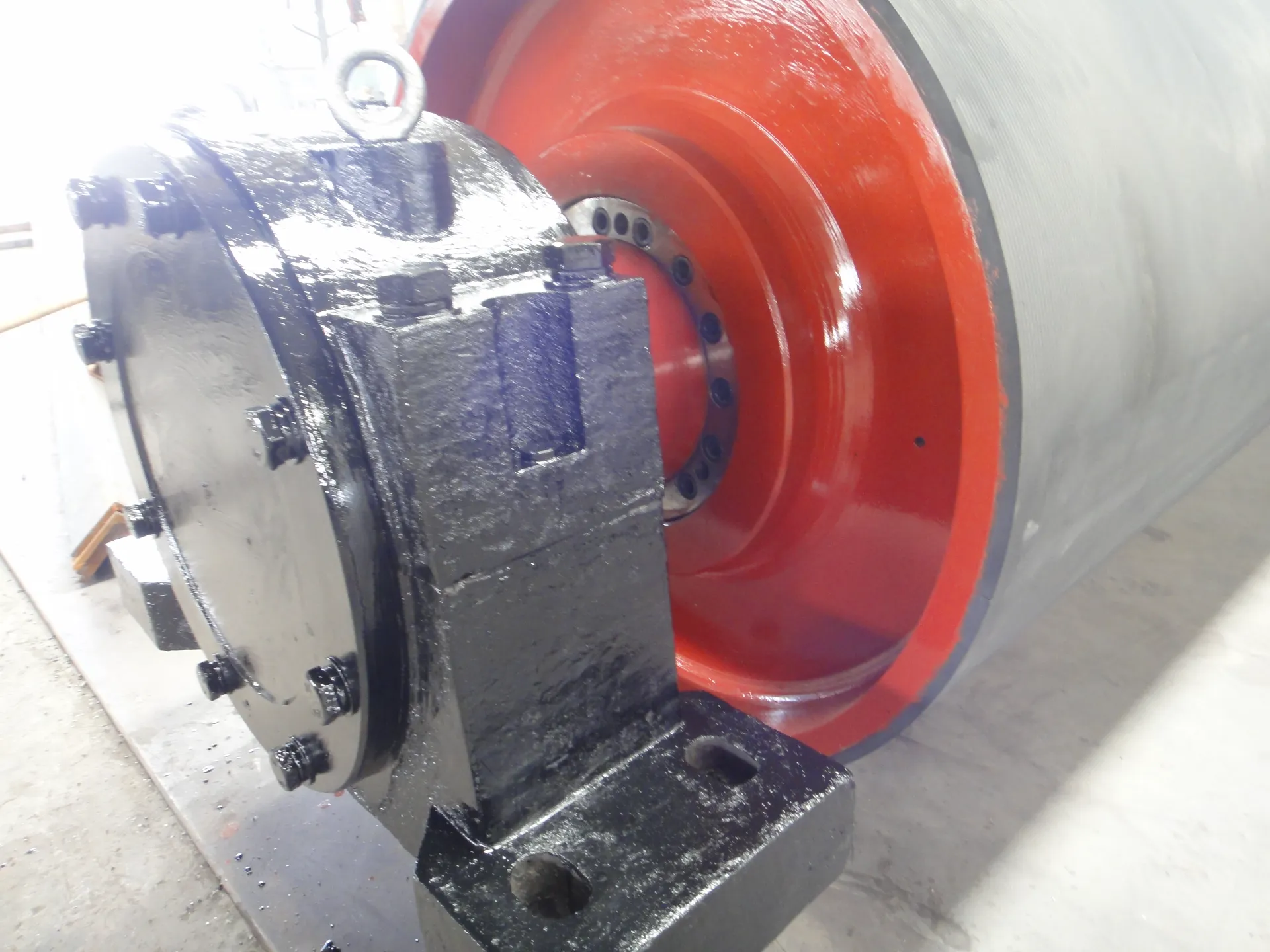
A picking idler is a type of idler roller set, strategically placed to support a conveyor belt in areas where materials are being loaded or removed. Unlike traditional idlers, picking idlers typically have a wider gap between the rollers, allowing for the easy removal or addition of materials without causing damage to the conveyor belt. This design is especially critical in industries such as mining, agriculture, and logistics, where the handling of bulk materials is frequent and variable in nature.
Experience in using picking idlers reveals that these components significantly reduce the wear and tear on conveyor belts. By minimizing the direct contact between the belt and materials, the picking idler helps in extending the life of the belt. This not only reduces maintenance costs but also minimizes downtime, a critical factor in high-volume industries where time equates to money.
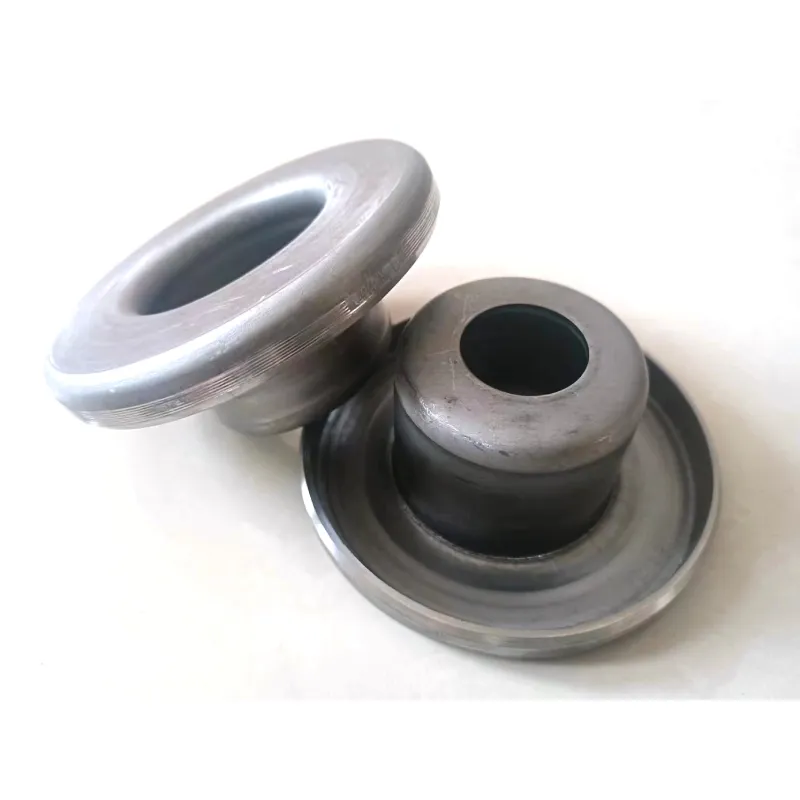
From an expertise perspective, the selection and installation of picking idlers require a thorough understanding of the system's dynamics. Factors such as the type of material being transported, the speed of the conveyor, and the environmental conditions must all be considered. For instance, heavier materials demand more robust idlers with superior load-bearing capacities, while corrosive environments require idlers made from specific materials to resist degradation.
picking idler
An authoritative insight into the use of picking idlers also emphasizes the importance of regular monitoring and maintenance.
Even the most well-constructed idlers are subject to wear over time. Regular inspections can preemptively identify issues such as misalignment or unusual vibrations, which could indicate a failing idler. Implementing a predictive maintenance schedule based on historical data can significantly enhance the reliability of the conveyor system and reduce unexpected failures.
The trustworthiness of sources discussing picking idlers is paramount for industry professionals seeking to optimize their conveyor systems. Manufacturers of industrial equipment often provide case studies and testimonials from reputable companies that have successfully implemented these components. Peer-reviewed journals and conferences focusing on industrial engineering can also offer valuable insights and validation of the latest advancements in idler technology.
Incorporating picking idlers into a conveyor system is not merely a mechanical decision but a strategic one. The right choice can lead to increased operational efficiency, reduced costs, and a competitive edge in the market. As industries continue to innovate and automate, the role of components like the picking idler becomes increasingly important. Future developments may see picking idlers equipped with smart sensors, providing real-time data on performance and further integrating them into the digital ecosystems of Industry 4.0.
In conclusion, the picking idler is more than a simple component; it is an essential element in optimizing conveyor systems. Through a combination of expert knowledge, authoritative resources, and trustworthy practices, industries can harness the full potential of their conveyor systems, ensuring efficiency and reliability in their operations.