The effective operation of belt conveyors relies heavily on two crucial components the head pulley and the tail pulley. These parts are vital for the smooth functioning, efficiency, and durability of conveyor systems across various industries. Understanding the core roles, maintenance practices, and technological advancements related to these components can significantly enhance your conveyor system's performance and longevity.
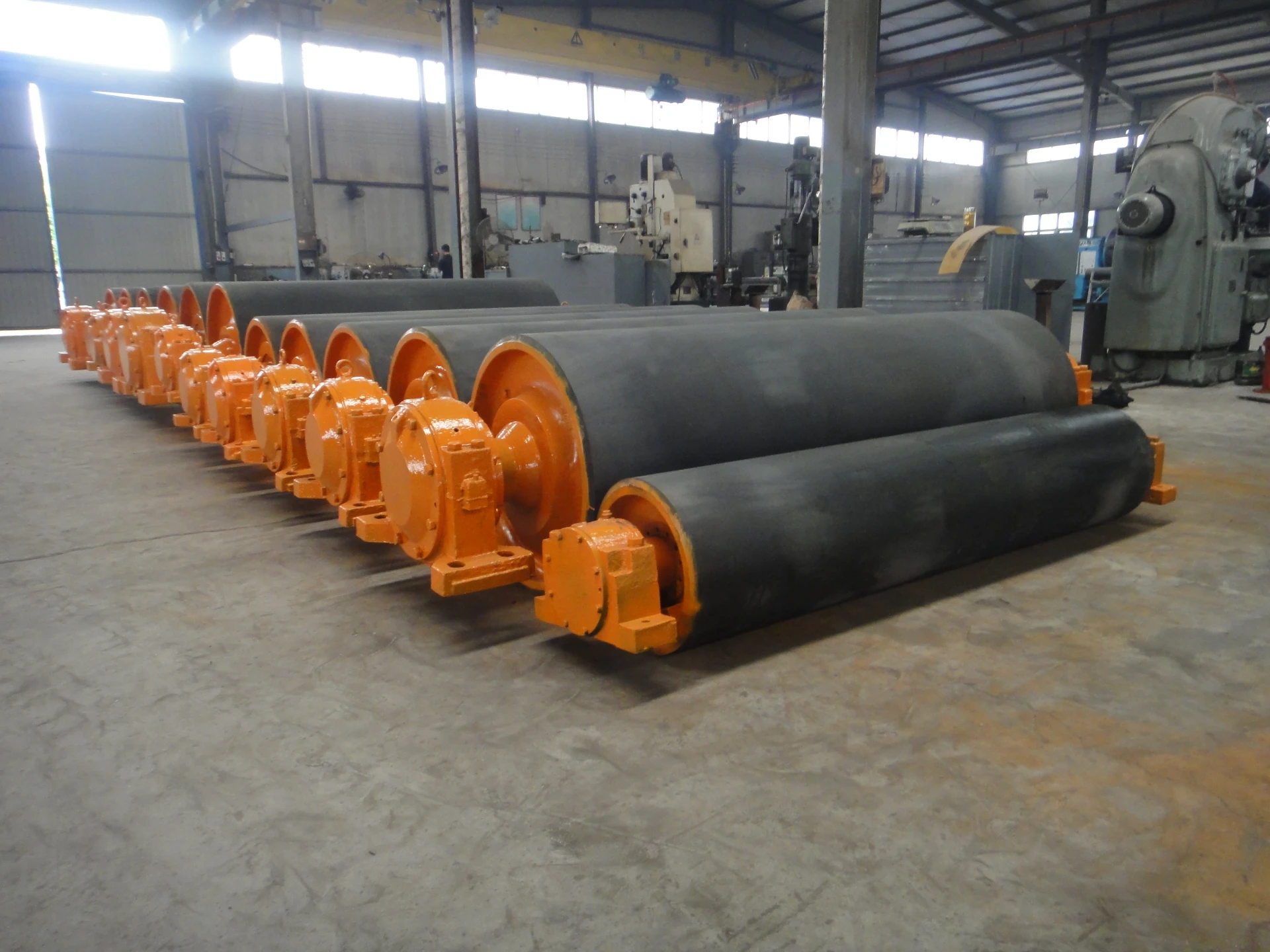
Head pulleys, positioned at the discharge end of the conveyor, play a critical role in driving the belt and maintaining tension. They are usually larger in diameter than tail pulleys and are often coated with lagging to enhance grip and prevent slippage. This reduces belt wear and energy consumption, contributing to an energy-efficient and cost-effective operation. It's essential to select a head pulley with the correct specifications for your system's load requirements, which are primarily determined by factors such as belt speed, load capacity, and environmental conditions.
Tail pulleys, on the other hand,
are located at the loading end of the conveyor. While they do not drive the belt, they contribute significantly to maintaining the belt's tension and alignment. This pulley typically has a simpler design but requires precise engineering to ensure smooth operation. Selecting the appropriate tail pulley involves considering factors such as belt width, material characteristics, and the presence of any corrosive elements in the transported materials.
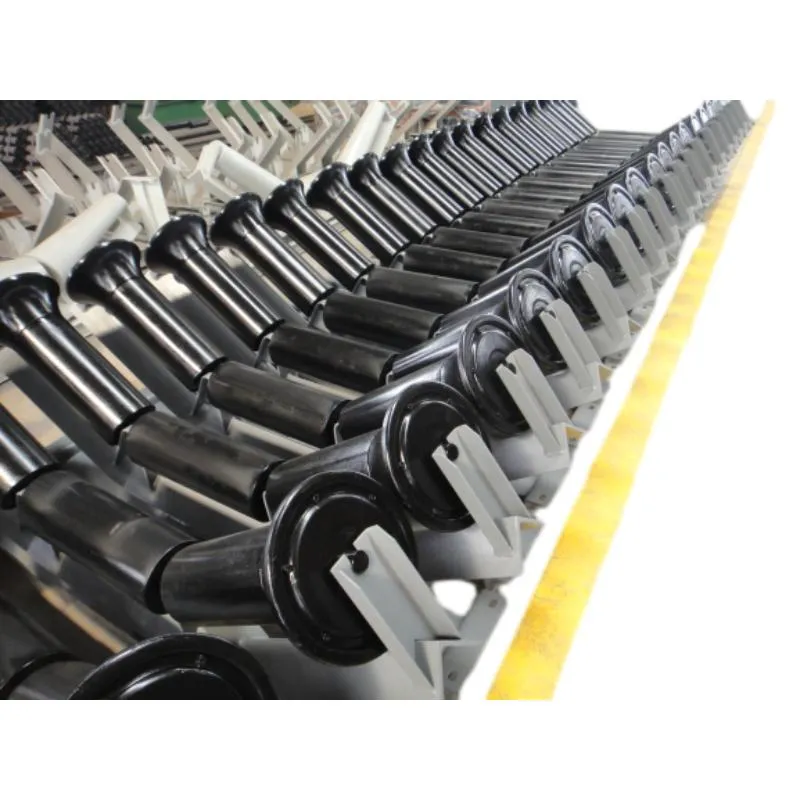
The material selection for both head and tail pulleys is crucial for their durability and efficiency. Materials commonly used include steel, rubber, and composite materials. Steel pulleys offer strength and durability, while rubber or ceramic lagging enhances traction and reduces wear. Advanced composite materials are gaining popularity for their lightweight properties and resistance to corrosion, especially in harsh or outdoor environments.
head pulley tail pulley for belt conveyor
Consistent and proactive maintenance of head and tail pulleys can prevent unexpected downtime and extend the lifespan of your conveyor system. Regular inspections should focus on signs of wear and tear, alignment issues, and surface condition. Lubricating bearings, checking for imbalances, and verifying proper tension alignment contribute to a seamless operation. Implementing a scheduled maintenance program can also automate these checks, ensuring they are performed regularly without compromising your operation's efficiency.
Technological advancements have significantly impacted the design and functionality of head and tail pulleys. Recent innovations include self-cleaning pulley systems, which prevent material build-up and reduce the risk of slippage, and the integration of sensors that monitor pulley health in real-time. These sensors can detect misalignment, uneven wear, and other potential issues, alerting maintenance teams before they escalate into a system failure.
Choosing the right head and tail pulleys involves not just understanding their roles but also recognizing the environmental and operational contexts of your conveyor system. Consulting with pulley manufacturers and engineers who specialize in conveyor systems can offer tailored solutions that align with your specific operational needs.
In conclusion, the optimal functioning of belt conveyors hinges on the selection and maintenance of head and tail pulleys. By prioritizing high-quality materials, adopting regular maintenance practices, and leveraging technological advancements, businesses can enhance efficiency, reduce operational costs, and ensure the longevity of their conveyor systems. Combining practical experience with technical expertise and authoritative insights ensures that your conveyor system remains reliable, efficient, and trustworthy in any industrial application.