In the realm of belt conveyor systems, head pulleys and tail pulleys are pivotal components that ensure the efficient movement of materials. Whether used in mining, manufacturing, or logistics, these pulleys play a critical role in the process, underscoring their importance in designing reliable and efficient material handling systems.
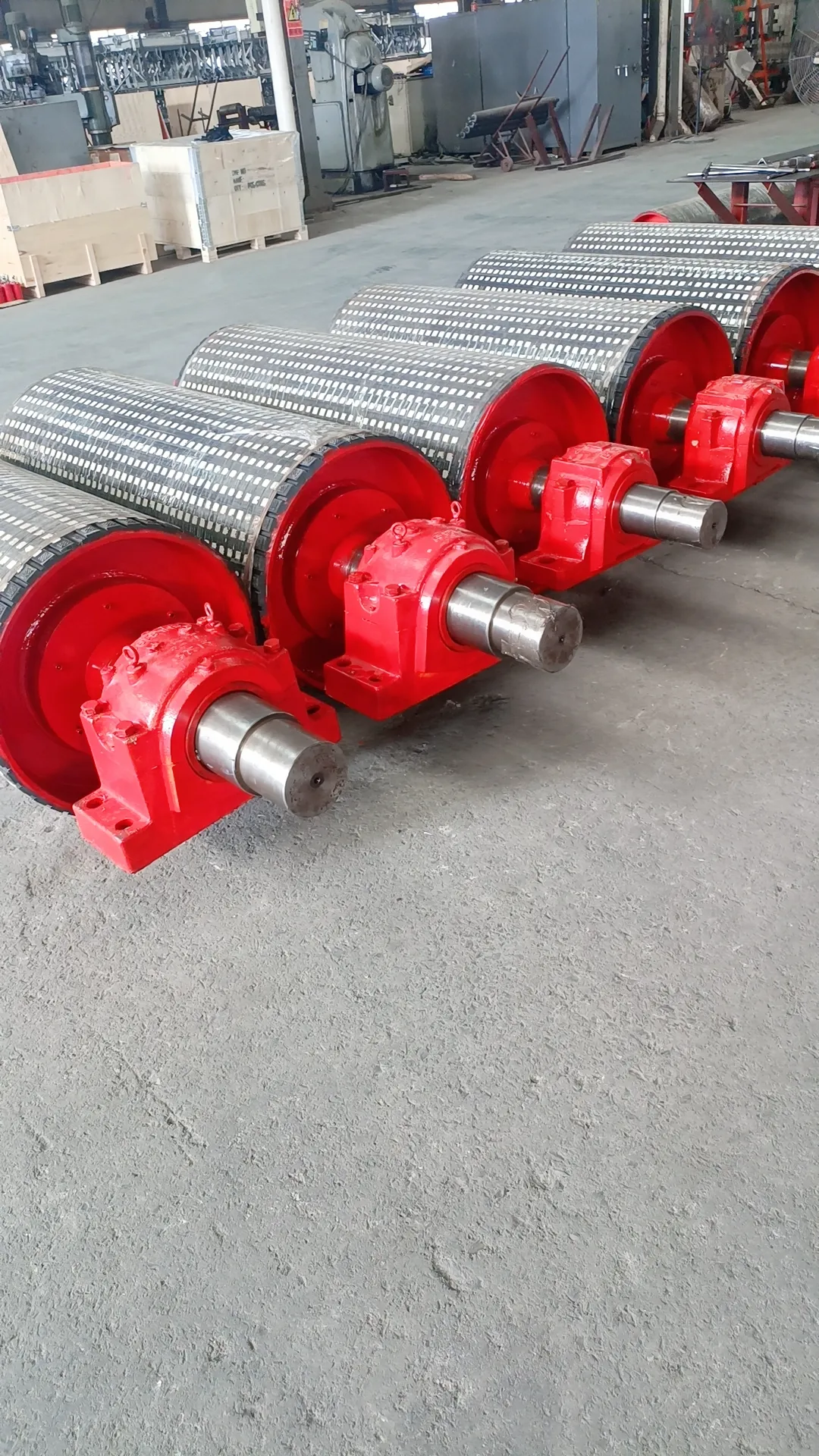
Head pulleys, generally located at the discharge end of a conveyor belt, are crucial because they drive the belt in the desired direction. The head pulley’s responsibility is not just about moving the belt; it is also about maintaining a suitable tension and alignment to minimize belt slip and avoid material spillage. This is where engineering expertise truly shines, crafting designs that cater to the specific needs of various industries. Material choice, pulley diameter, and lagging are all factors that experienced engineers consider when optimizing the head pulley for operational demands. For instance, rubber lagging might be chosen for its high friction and wear resistance, ensuring long-term effectiveness even in harsh environments.
On the other end,
the tail pulley is located at the feed point or at the return side of the conveyor. Its primary purpose is to support the belt and maintain appropriate tension as it cycles between the head pulley and itself. A well-designed tail pulley is fundamental to the smooth operation of the conveyor system, helping to stabilize the belt as it returns. Expertise in pulley design is evident here too, as the tail pulley must handle variable loads without succumbing to excessive wear or misalignment. Using advanced materials and precisely engineered bearings, manufacturers construct tail pulleys resilient enough to endure significant operational demands while minimizing maintenance needs.
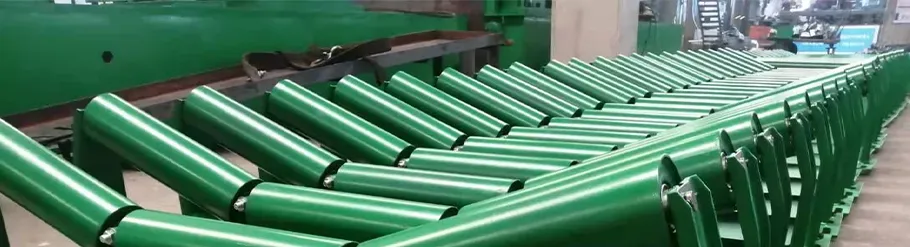
Professional experience in optimizing conveyor systems highlights the balance between durability and efficiency. An essential aspect of this is understanding the complete conveyor system's stressors and configuring the pulleys accordingly, which can involve using modern analytical tools to predict wear patterns and simulate operational conditions. Performing these analytics with accuracy demands authoritative knowledge in both material science and mechanical engineering.
head pulley tail pulley for belt conveyor
The authoritative voice of industry standards plays an important role when fabricating head and tail pulleys. Compliance with recognized standards ensures these components meet safety and performance benchmarks vital for industry trustworthiness. Standards such as CEMA or ISO offer guidelines on dimensions, tolerances, and material specifications, assisting manufacturers in delivering reliable and quality products. Additionally, having industry-specific certifications can further attest to a manufacturer’s dedication to safety and quality, enhancing brand trustworthiness in the marketplace.
Trust in these crucial conveyor components also relies heavily on real-world application and performance history. Case studies often speak volumes, demonstrating how particular pulley designs have withstood various operational challenges. Whether it’s a mining operation where pulleys deal with abrasive materials or a processing plant that requires high-speed operations, documenting performance over time builds confidence with stakeholders that these components can stand the test of time.
Investing in high-quality head and tail pulleys is fundamentally about improving operational efficacy and reducing long-term costs. This approach resonates with businesses aiming for optimized performance and a competitive edge. Trustworthiness is correlated with a manufacturer’s transparency in the production process, material sourcing, and post-purchase support. Offering warranties and comprehensive service plans are assurance markers that reflect a commitment to quality and customer satisfaction.
The journey towards mastering head pulley and tail pulley optimization is a testament to the bond between engineering prowess and industrial needs. Realizing their potential demands not only experience and authoritative knowledge but also a forward-thinking approach to design and service. This makes these components central to elevating the standards for belt conveyor systems, ensuring reliability and efficiency in every application they touch.