The drum pulley plays a pivotal role in various industrial applications, particularly within conveyor systems and material handling equipment. This indispensable component facilitates the movement and redirection of conveyor belts, ensuring smooth and efficient operations. With years of experience in the industry, I've seen firsthand the transformative power of well-designed drum pulleys in enhancing system productivity and minimizing operational downtimes.
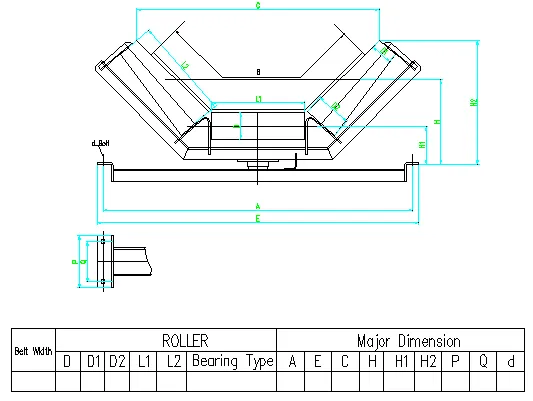
A drum pulley, by definition, is a cylindrical component that's often situated at either end of a conveyor belt. This strategic placement allows it to guide the belt's movement seamlessly, reducing wear and tear. The key to an effective drum pulley lies in its construction, durability, and the materials used. Constructed typically from high-strength steel or even alloys, drum pulleys are designed to withstand immense pressure and friction, translating to extended longevity and reliability.
Choosing the right drum pulley requires a nuanced understanding of your specific operational needs. It's imperative to evaluate factors such as the pulley’s diameter, face width,
and shaft size. These dimensions are not arbitrary; they are tailored to align with the belt’s specifications and the system’s load capacity. A misjudgment in these metrics can lead to inefficient operations and potentially hazardous belt slippage.
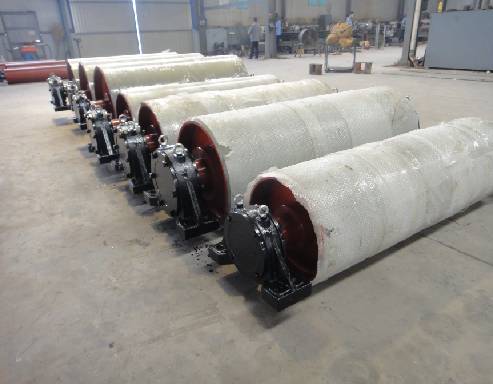
My expertise in this field has taught me to emphasize the importance of pulley lagging - the coating applied to the pulley’s surface to enhance grip and reduce slippage. Rubber lagging, in particular, is lauded for its high friction coefficient and durability. However, ceramic lagging is becoming increasingly popular due to its exceptional resistance to abrasion and improved gripping power, particularly in wet conditions. This is essential for ensuring the conveyor belt maintains optimal performance even under challenging environmental conditions.
drum pulley
The authority of a drum pulley within an industrial operation is further underscored by its role in maintaining belt alignment. A misaligned belt can lead to significant operational inefficiencies and pose safety risks. Incorporating features like crowned pulleys and adjustable tensioning mechanisms can considerably improve alignment, ensuring that your operation runs smoothly without unnecessary interruptions.
Trustworthiness in drum pulleys also depends on their compliance with industry standards and quality certifications. These standards are indicative of the pulley’s quality and its ability to perform reliably under strenuous conditions. For instance, adherence to ISO 9001 certification showcases a commitment to quality management practices. Engaging with manufacturers who uphold these standards is crucial in establishing and maintaining a trust-based relationship.
In my professional journey, I have seen companies transform their operational efficiencies by investing in top-tier drum pulleys. Not only do these components enhance system performance, but they also provide a substantial return on investment through reduced maintenance costs and prolonged equipment lifespan. Whether in mining, manufacturing, or logistics, the strategic implementation of high-quality drum pulleys is often a game-changer.
In conclusion, drum pulleys are not merely passive components in a conveyor system; they are vital for achieving operational excellence. A well-chosen pulley, tailored to your specific needs and rigorously maintained, can provide unparalleled advantages in efficiency and longevity. By prioritizing factors such as construction materials, lagging options, and compliance with industry standards, you can elevate your entire operation’s performance. As the technological landscape advances, staying informed and proactive about the latest developments in drum pulley technology will continue to be essential for maintaining a competitive edge in industrial operations.