Drum pulleys play an indispensable role in the effectiveness and efficiency of various industrial operations, particularly in conveyor systems where reliability and precision are crucial. While their significance is often overshadowed by their seemingly mechanical simplicity, the truth is that these components hold the key to seamless operational workflows.
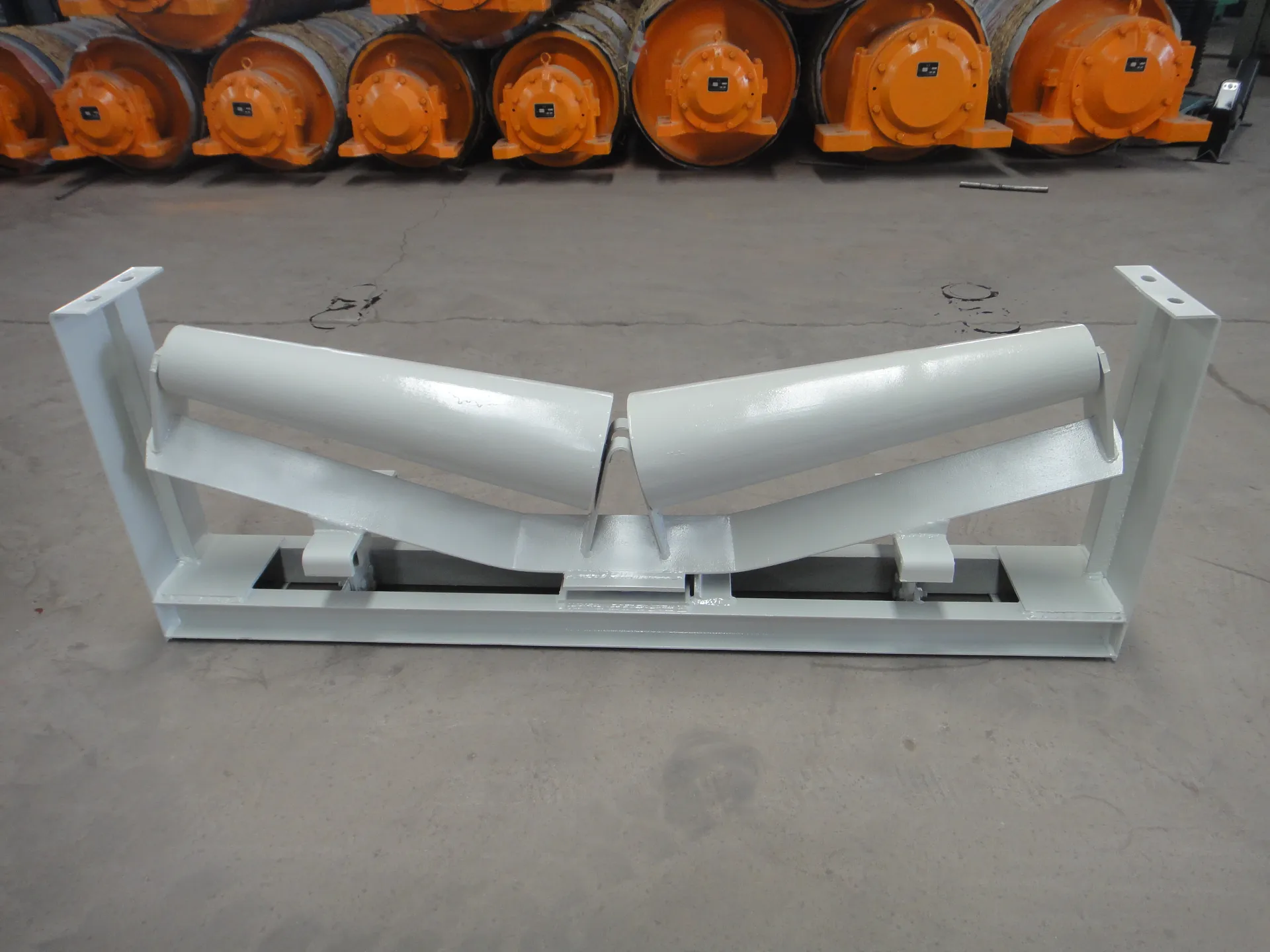
Imagine an extensive conveyor belt system in a bustling manufacturing plant. Here, drum pulleys are pivotal, transforming what would otherwise be manual labor into a streamlined automated process. These cylindrical devices work as power transmission units, guiding the conveyor belt along its looped path with precision and control.
From my extensive experience in the industrial machinery sector, selecting the right drum pulley is paramount. The choice governs not just the efficiency of the conveyor system but also its lifespan and maintenance requirements. A miscalculated choice can lead to increased wear-and-tear, energy inefficiencies, and unplanned downtimes, ultimately impacting the bottom line.
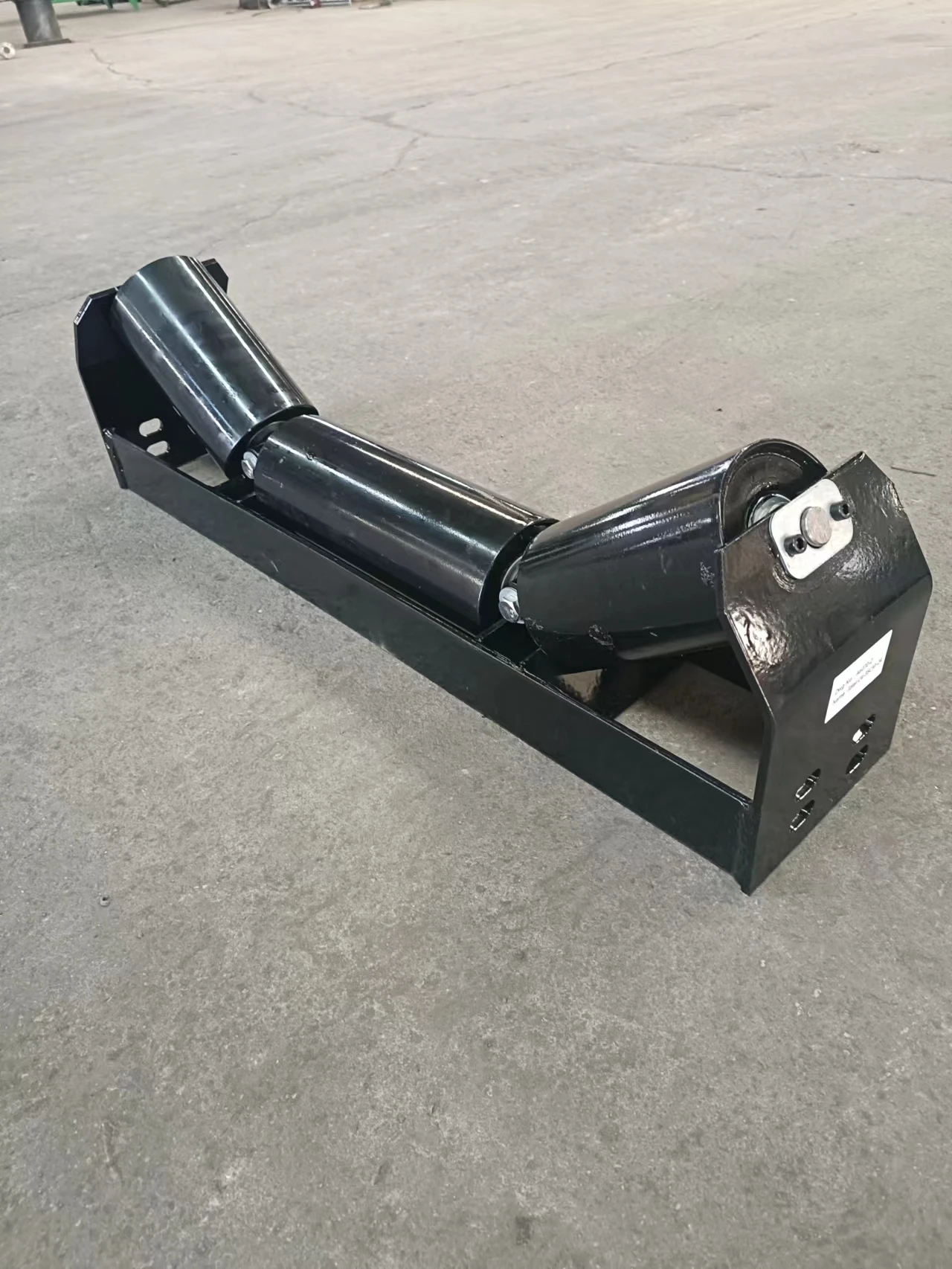
Understanding the nuances of drum pulleys encompasses a few critical parameters.
One central aspect is the material selection. For example, steel drum pulleys provide unmatched strength and durability, making them ideal for heavy-duty applications. They are, however, more susceptible to corrosion if not appropriately treated. Alternatively, aluminum pulleys, though lighter and more resistant to corrosion, may not offer the same degree of durability under extreme conditions.
The covering or lagging on a drum pulley is another influential factor. Rubber lagging is commonly preferred due to its traction-enhancing properties. It provides the necessary friction that assures a firm grip of the conveyor belt, hence preventing slippage. Additionally, ceramic lagging options have been gaining popularity due to their enhanced traction and superior wear resistance, thus offering a longer operational life.
Having spent years collaborating with engineers and operational managers, I've observed firsthand the impact that innovation in pulley design brings to industrial efficiency. Modern designs now include self-cleaning drum pulleys that reduce material build-up, significantly cutting down maintenance time and cost.
drum pulley
It's not just the physical aspects of the drum pulley that command attention; understanding the application requirements is equally crucial. The maintenance team’s expertise, coupled with strategic supplier relationships, builds a foundation of reliability and trust. Regular training and updates on the latest technologies enable maintenance teams to preempt issues, ensuring longevity and consistent performance.
Moreover, the integration of smart sensors with drum pulleys marks a significant advancement. These sensors allow real-time monitoring of pulley conditions, predicting potential failures before they occur. By doing so, companies can transition from reactive to predictive maintenance strategies, enhancing operational reliability and scheduling maintenance only when necessary.
A deep dive into the technical specifications, like bearing and shaft sizes, also reveals much about a pulley’s suitability for a given application. Precision in these areas reduces operational friction and supports higher load capacities. Every element must align with the conveyor belt’s demands and the broader operational context.
With a profound grasp of drum pulleys and their integration into conveyor systems, we recognize not just their functional importance but also the strategic value they add to operations. Industry professionals must leverage their knowledge to guide conscious decisions that reflect both immediate and long-term requirements.
When investing in drum pulleys, quality assurance from established manufacturers ensures compliance with industrial standards and greater peace of mind. Certifications and testing protocols are indicators of a manufacturer’s commitment to quality and safety, factors that cannot be overlooked in the pursuit of operational excellence.
While drum pulleys may seem like a humble component of industrial machinery at first glance, their impact stretches far beyond what meets the eye. Expertise and experience reveal their true potential, underscoring their contribution to productivity, safety, and sustainable operations. Trust in quality, expertise, and continuous learning forms the cornerstone of successful integration and optimization of these silent workhorses in the industry.