Drive rollers for conveyors are integral components in materials handling, providing the necessary motion and direction within a conveyor system. These robust and versatile pieces of equipment are designed to meet the rigorous demands of industrial environments, ensuring efficiency and productivity across various sectors.
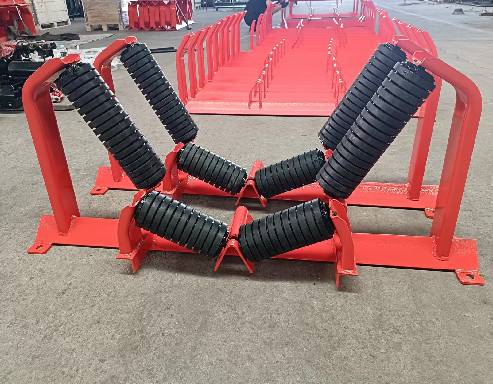
Selecting the right drive rollers is crucial for businesses seeking to optimize their conveyance processes. Expertise in the construction and operation of these rollers can significantly enhance system performance. Drive rollers are not merely cylindrical components; they are engineered with precision to fulfill specific functions. They typically consist of a metal core coated with a durable material that delivers friction and traction. This precise construction is vital for withstanding the weight and frequency of items transported in myriad industries such as manufacturing, food processing, and mining.
It is essential to understand the mechanics behind drive rollers to appreciate their role fully. At their core, these components transfer rotational power from a motor to convey items along a belt or track. The efficiency of drive rollers directly influences the speed, load capacity, and direction control of a conveyor system. A well-chosen drive roller can seamlessly handle variables such as load weight and material type, ensuring minimal downtime and operational disruption.
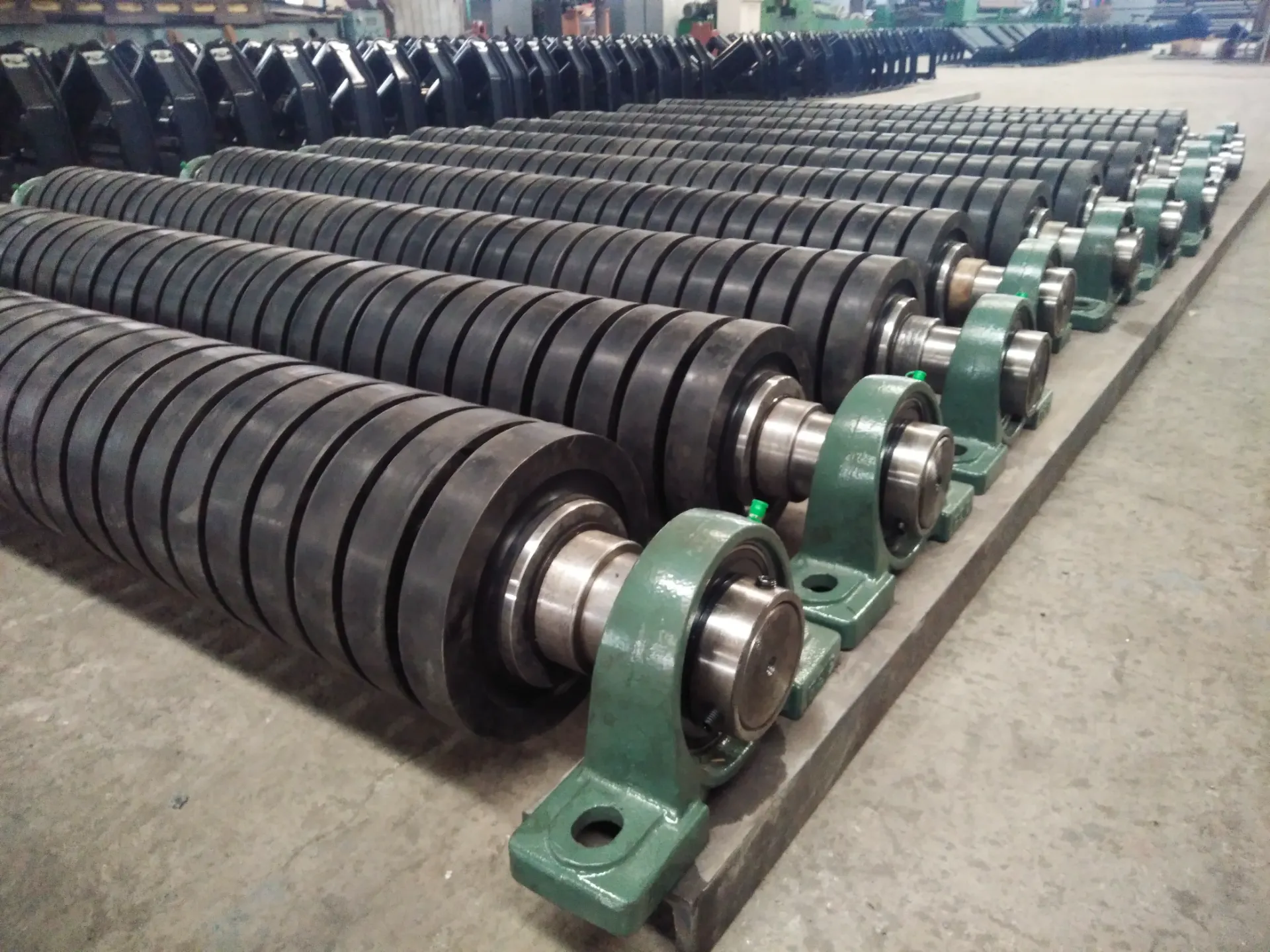
The drive roller's surface material is often coated in rubber, polyurethane, or other specialized compounds to offer different levels of grip and wear resistance. Each material has distinct properties that influence the roller's performance, dictating suitability for specific applications. For example, rubber-coated rollers might be chosen for their high levels of traction and quiet operation, making them ideal for environments where noise reduction is a priority. On the other hand, polyurethane is preferred in scenarios requiring extra durability and resistance to wear and tear, especially in demanding industrial settings.
drive rollers for conveyors
Moreover, professional assessment and installation of drive rollers can significantly impact the lifespan and reliability of a conveyor system. An authoritative understanding of drive roller specs—such as diameter, shaft size, and surface finish—is necessary to ensure compatibility with existing systems and to achieve desired conveyor performance. Misalignment or improper specifications can lead to premature wear, reduced efficiency, and operational failures, highlighting the necessity for expert guidance and precise engineering.
Trustworthiness in drive roller selection and maintenance comes from sourcing high-quality components from reputable manufacturers. Ensuring that these components meet industry standards and certifications guarantees safety and reliability. Regular maintenance and inspection further extend their longevity, preventing costly repairs and downtime. Businesses should prioritize suppliers that provide comprehensive support, offering insights into the proper use, maintenance schedules, and troubleshooting to uphold operational readiness.
Ensuring trust in the materials and assembly of drive rollers also involves understanding where they originate. Manufacturing processes adhering to stringent quality controls provide assurance that the rollers will perform reliably under specified conditions. An authoritative supplier should offer detailed documentation on the manufacturing process, material origins, and quality checks, enhancing buyer confidence.
In summary, drive rollers for conveyors are not just about moving items from one point to another; they are about ensuring smooth, efficient, and reliable operations across industrial environments. With the right expertise and authority, businesses can select the appropriate drive rollers, optimize their conveyor systems, and ensure trustworthiness through stringent quality standards and professional maintenance. These tenets form the backbone of effective conveyor system management, minimizing operational disruptions and maximizing throughput.