In the world of industrial systems, conveyor pulley parts stand as pivotal components in the movement and processing of materials across a myriad of operations. Their functionality is critical, ensuring that businesses meet rigorous demands with efficiency and reliability. Understanding the nuances of these components can significantly impact the operation of conveyor systems, maximizing both productivity and machinery lifespan.
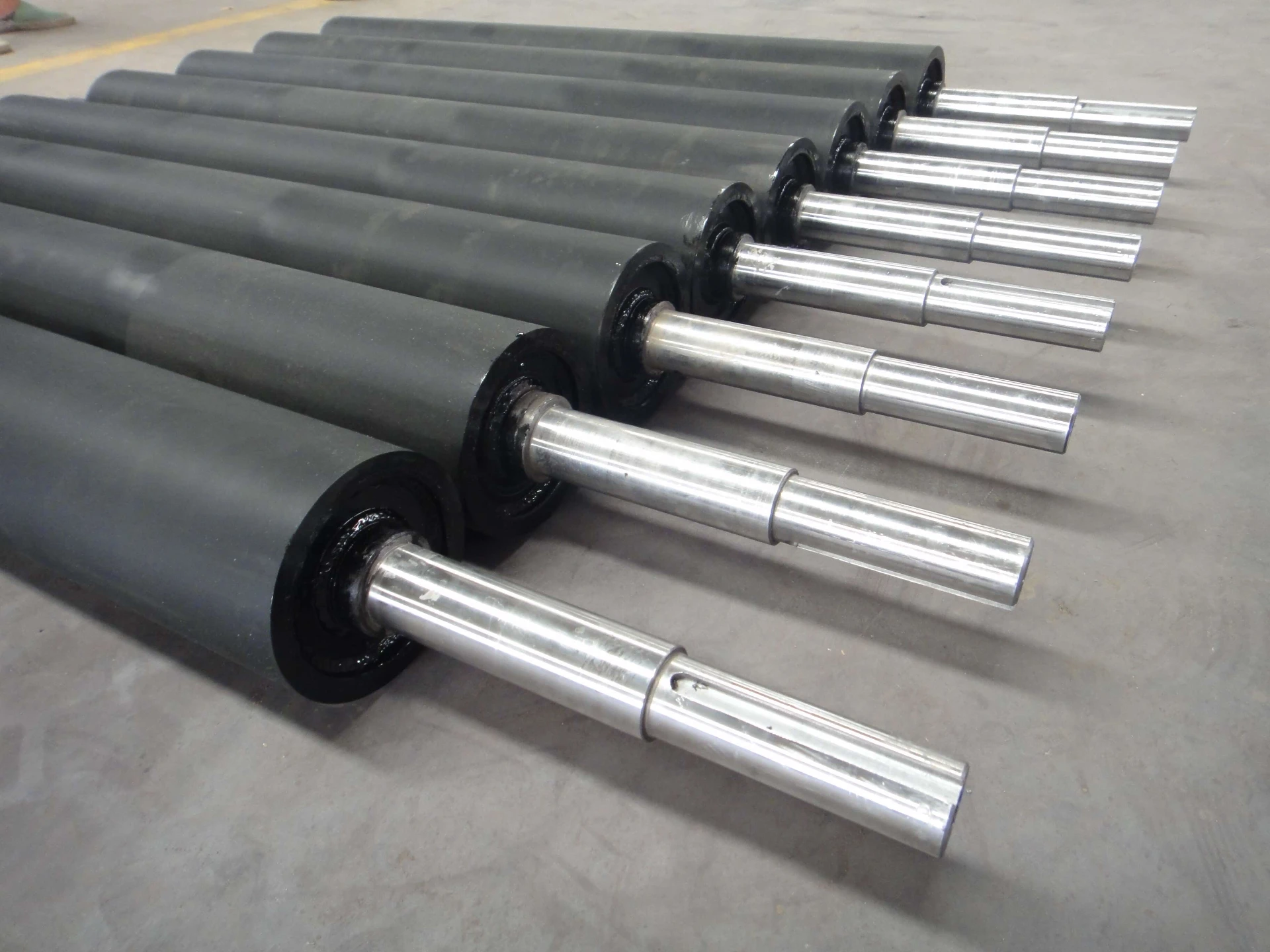
Central to any conveyor system is the drum pulley, often referred to as the heart of the system. These pulleys are tasked with driving the belt, and consequently, the entire conveyor structure. Constructed from robust materials such as steel or aluminum, drum pulleys must withstand immense tension while maintaining alignment to avoid system disruptions. The quality of the drum pulley directly correlates with the system’s performance; hence choosing a pulley tailored to specific operations is crucial.
Another vital component is the wing pulley, designed explicitly for environments where material build-up is a challenge. These pulleys feature structured wings that effectively release excess materials, reducing the risk of belt misalignment and undue wear. In sectors handling raw and sticky materials, such as in mining or agriculture, wing pulleys play an indispensable role by ensuring that operations continue smoothly without frequent interruptions.
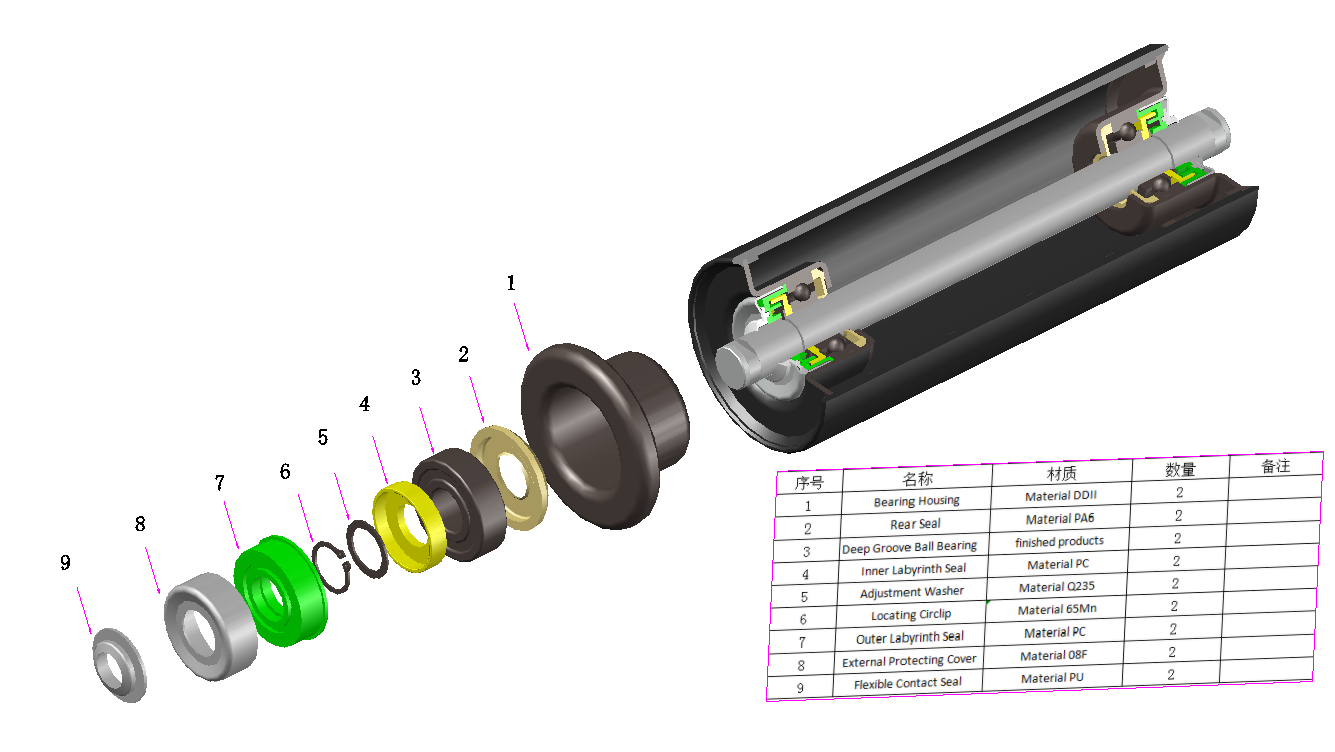
Lagging is a targeted enhancement designed to improve the frictional grip between the pulley and the conveyor belt. By providing a non-slip surface, lagging markedly heightens traction, particularly beneficial in wet conditions or environments with high wear rates. Moreover, lagging can be engineered from various substances such as rubber, ceramics, or a combination of both, catering to the specific needs of different industrial applications, thus enhancing operational precision and efficiency.
Equally critical are the bearing housings, which envelope the pulley shaft. These components provide not only essential support to the rotating shaft but are engineered to minimize mechanical failures by absorbing radial and axial loads. High-quality bearing housings help maintain the alignment of the shafts, reducing vibrations and ensuring the conveyor system operates with minimal noise and maximal stability.
conveyor pulley parts
The importance of precise alignment cannot be overstated when it comes to conveyor systems, and here, pulleys serve as invaluable allies. The proper installation and maintenance of take-up pulleys, for instance, ensure consistent belt tension, preventing slip and avoiding unnecessary straining of the motor. The correct tension is achieved through systems that allow for automatic adjustments, particularly useful in long conveyor belts subjected to variable loads and temperatures.
Material choice and engineering do not solely determine the success of conveyor pulley parts; regular maintenance also plays a critical role. Routine inspections can identify early signs of wear such as belt slippage, unusual noise, or misalignment, allowing timely interventions that prevent costly machine downtime. Maintenance plans should include regular checks of pulley balance, bearing lubrication, and lagging condition, ensuring components remain in peak condition.
Innovation in conveyor pulley technology is an ongoing journey, with manufacturers constantly optimizing designs to improve performance. For instance, the integration of sensors for predictive maintenance provides real-time data, which can substantially aid in preemptive diagnosing of potential issues. Such smart technologies help in making informed decisions, reinforcing the system’s operational efficacy, and ultimately enhancing the return on investment for businesses relying on these essential components.
In conclusion, conveyor pulley parts are far more than mere mechanical elements. Their expert design and reliability are at the core of efficient material handling systems. The components discussed—from drum and wing pulleys to lagging and bearing housings—each play specialized roles that collectively ensure smooth and efficient operations in industrial environments. By investing in quality and incorporating regular maintenance along with new technologies, businesses can secure a competitive edge, optimizing their conveyor systems for future challenges.