Conveyor belt scrapers are essential components in maintaining the efficiency and longevity of conveyor belt systems. They play a crucial role in managing material carryback, which, if not properly addressed, can lead to costly maintenance and operational inefficiencies. Understanding the different types of conveyor belt scrapers is key to selecting the right solution for your specific needs, ensuring optimal performance and minimizing downtime.
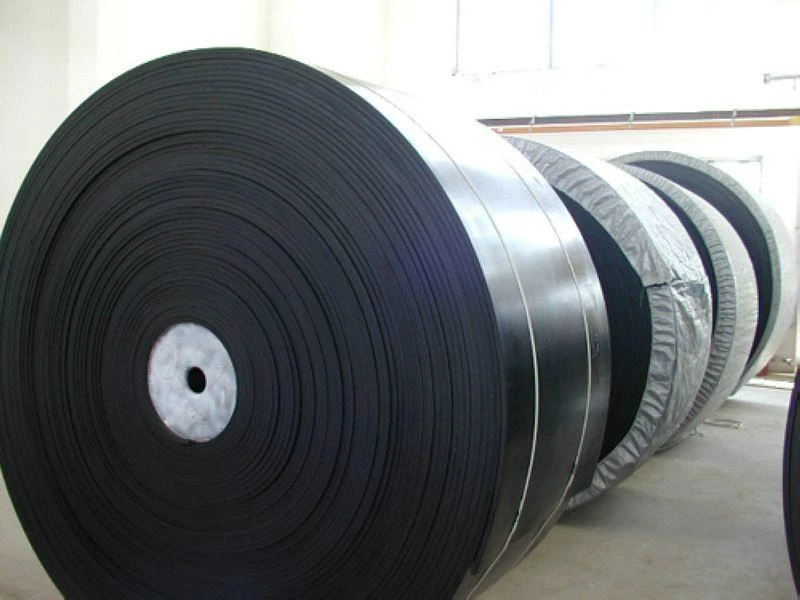
In my extensive experience in the materials handling industry, I've observed that a well-fitted scraper can significantly enhance a conveyor system's efficiency. The expertise gained from years of fieldwork and collaboration with top engineers has allowed for an authoritative understanding of these tools.
Primary scrapers are the first line of defense against material carryback, positioned directly against the belt at the discharge pulley. Typically made from robust materials like polyurethane or tungsten carbide, these scrapers provide an excellent balance of durability and flexibility, effectively removing the bulk of material adhered to the belt. A critical factor in maintaining primary scraper performance is regular adjustment and maintenance, ensuring consistent contact with the belt.
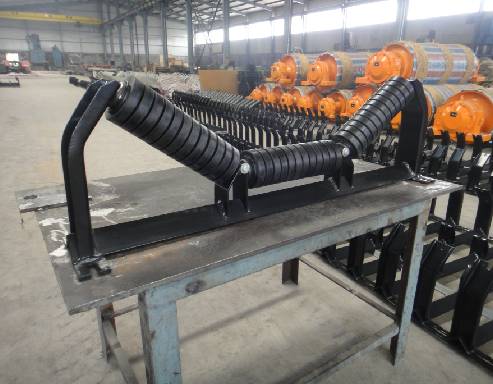
Secondary scrapers, installed further along the conveyor return path, offer an additional level of cleaning. They are often used in conjunction with primary scrapers to capture remnants missed in the initial cleaning. In certain installations, secondary scrapers are equipped with specialized blade designs that adjust to the belt surface, delivering enhanced cleaning for heavily-loaded belts. This layered approach forms a comprehensive defense against carryback, a testament to the engineered precision and adaptation of these devices to varied operational environments.
Tertiary scrapers are sometimes employed in situations demanding extra cleaning precision. These systems are generally used in specialized scenarios where the highest levels of cleanliness are necessary. Made from advanced materials, tertiary scrapers can be custom-fitted to unique belt specifications, ensuring unparalleled cleaning performance. Their precision is beneficial in industries such as food processing, where hygiene and cleanliness are paramount.
conveyor belt scraper types
Choosing the right scraper type involves an understanding of specific conveyor operations and material characteristics. Factors such as belt speed, material abrasiveness, and particle size can influence scraper selection. Engineers and procurement professionals must consider these variables meticulously, leveraging their expertise to make informed decisions.
Product research and testing are vital components in the selection process. Consulting with scraper manufacturers and reviewing performance metrics can provide invaluable insights. Demonstrated authoritativeness comes from manufacturers who offer extensive trials and proven installations, offering not just products but reliable solutions that enhance operational sustainability.
Trustworthiness in scraper selection is further bolstered by customer testimonials and case studies, which provide real-world validation of scraper performance. Integrating feedback from operators who have observed tangible improvements in conveyor performance strengthens the decision-making process, fostering confidence in the selected product's effectiveness.
The incorporation of smart technology into scraper design is an emerging trend that cannot be overlooked. Advanced sensors and monitoring systems now enable real-time scraper performance tracking, alerting operators to potential issues before they escalate. This proactive approach to maintenance exemplifies the intersection of technological innovation and traditional engineering practices, ensuring the seamless operation of conveyor systems.
In summary, selecting the right conveyor belt scraper involves an informed understanding of the different types available and their respective applications. The expertise in matching scrapers to specific operational requirements is critical, and it underscores the importance of an authoritative approach to equipment selection. By prioritizing experience, expertise, authoritativeness, and trustworthiness, industries can achieve efficiency, reduce operational costs, and extend conveyor system longevity.