Conveyor belt drive rollers are integral components in conveying systems, serving as the heartbeat that keeps production lines running smoothly. As a specialist in this field, you quickly realize that choosing the right roller is not merely about functionality—it involves a deep understanding of mechanics, materials, and efficiency optimization.
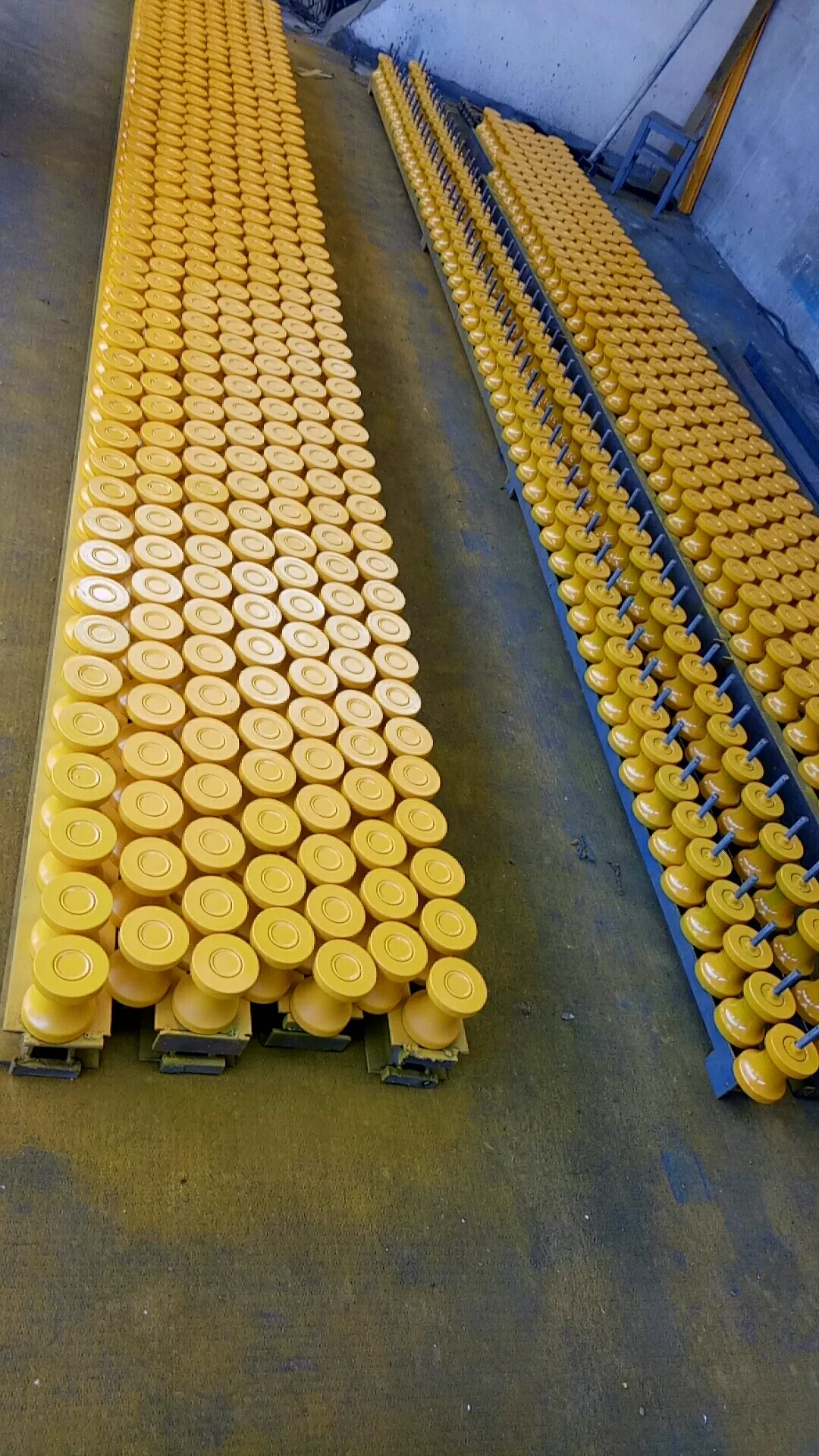
When assessing conveyor belt drive rollers, the first aspect to consider is the material composition. Rollers are typically manufactured from robust materials such as stainless steel, aluminum, or composite materials, each selected based on specific operational environments. Stainless steel, renowned for its durability and resistance to corrosion, is ideal for food processing or outdoor applications. In contrast, aluminum is valued for its lightweight properties, enhancing energy efficiency, while composite materials offer versatile applications due to their adaptability and cost-effectiveness.
Expertise in this domain reveals that precision in manufacturing is paramount. The roller must maintain exact concentricity and balance to minimize vibrations, which can otherwise lead to unscheduled downtimes or premature wear and tear. An investment in high-precision machinery ensures the rollers meet strict tolerances, contributing to the seamless operation of complex systems.
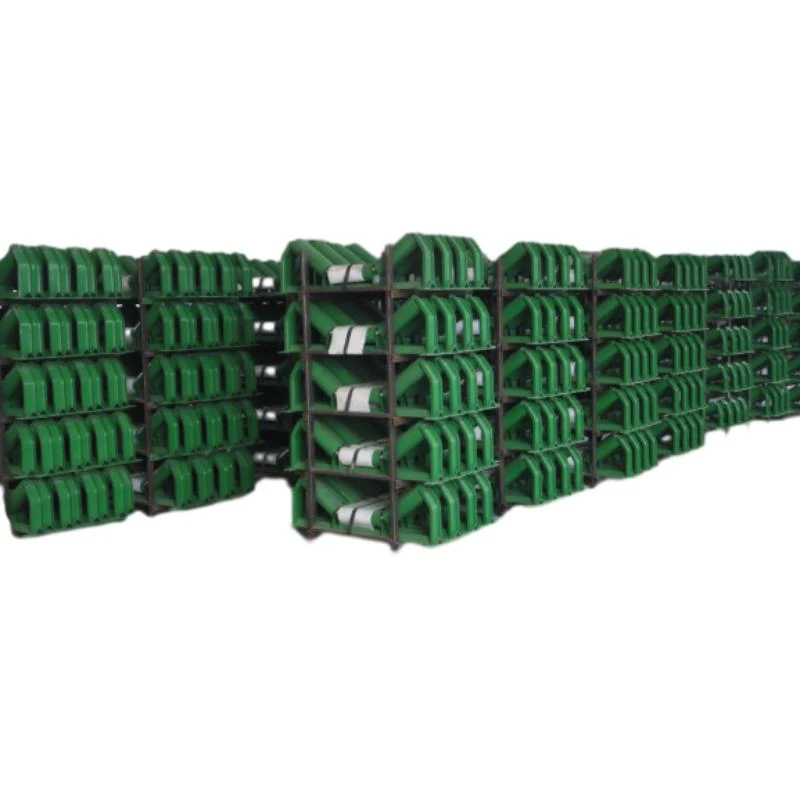
When selecting drive rollers, another critical factor is understanding the dynamic forces involved. The torque and rotational speed must be perfectly aligned with the conveyor's intended load and speed. Underestimating these forces could lead to slippage or excessive wear. Therefore, calculating the maximum load capacity and using advanced CAD software to simulate real-world operational conditions are essential steps in the design phase.
The surface finish of the drive rollers also deserves close attention. Textured or grooved surfaces enhance grip, reducing the risk of belt slippage. Meanwhile, smooth surfaces might be preferred in applications where the product integrity must be preserved, minimizing contact abrasions or unnecessary friction.
conveyor belt drive rollers
Authoritative suppliers of conveyor belt drive rollers offer not only top-grade components but also consultancy services. They work closely with industrial clients to customize solutions, ensuring that the rollers are akin to tailored suits, perfectly fitting the project's unique demands. From advising on motor compatibility to suggesting specific bearings, these suppliers provide a comprehensive package of services that underscore their authority in the industry.
Trust in a product often stems from rigorous testing and quality assurances. Leading manufacturers conduct an exhaustive suite of tests, including fatigue testing, thermal resistance evaluations, and friction assessments, to certify their rollers' resilience and operational longevity. They certify compliance with international standards such as ISO9001, instilling confidence that the product will perform reliably under specified conditions.
Security in choice is further validated by client testimonials and case studies that reflect real-world applications. Documenting experiences of enhanced productivity and reduced maintenance costs following the installation of high-quality rollers builds a narrative of trust and expertise. Furthermore, companies that provide transparent datasheets and prompt customer support strengthen their position as trustworthy partners.
In conclusion, conveyor belt drive rollers are much more than simple components; they are pivotal in the orchestration of a seamless production process. Understanding the intricate balance of materials, design precision, and operational efficiency defines the expertise necessary to choose the right rollers. Professionals and industrialists who recognize the importance of these factors are those who can excel in optimizing both performance and cost-efficiency, crafting an unyielding trust in their chosen solutions.