The Evolution of Idler Rollers Types and Applications
In the realm of conveyor systems, idler rollers play a crucial role in ensuring smooth and efficient operation. These rollers, typically composed of a cylindrical tube and bearings, support the weight of conveyed materials and reduce friction between the belt and the supporting surface. Over time, the design and functionality of idler rollers have evolved significantly, leading to the development of various types catering to specific industrial needs.
One of the most common types of idler rollers is the plain idler roller. These rollers consist of a simple cylindrical tube that rotates on its bearings, providing support and guidance to the conveyor belt. Plain idler rollers are widely used in applications where the conveyed material has low to moderate friction, such as in food processing or light manufacturing facilities.
Another type of idler roller is the flanged idler roller. As the name suggests, these rollers have flanges on either end to prevent the belt from slipping off the roller. Flanged idler rollers are commonly used in applications where the belt needs to be tightly secured, such as in mining or heavy industry.
For environments where the conveyed material is particularly abrasive or corrosive, special types of idler rollers with protective coatings or materials are used
For environments where the conveyed material is particularly abrasive or corrosive, special types of idler rollers with protective coatings or materials are used
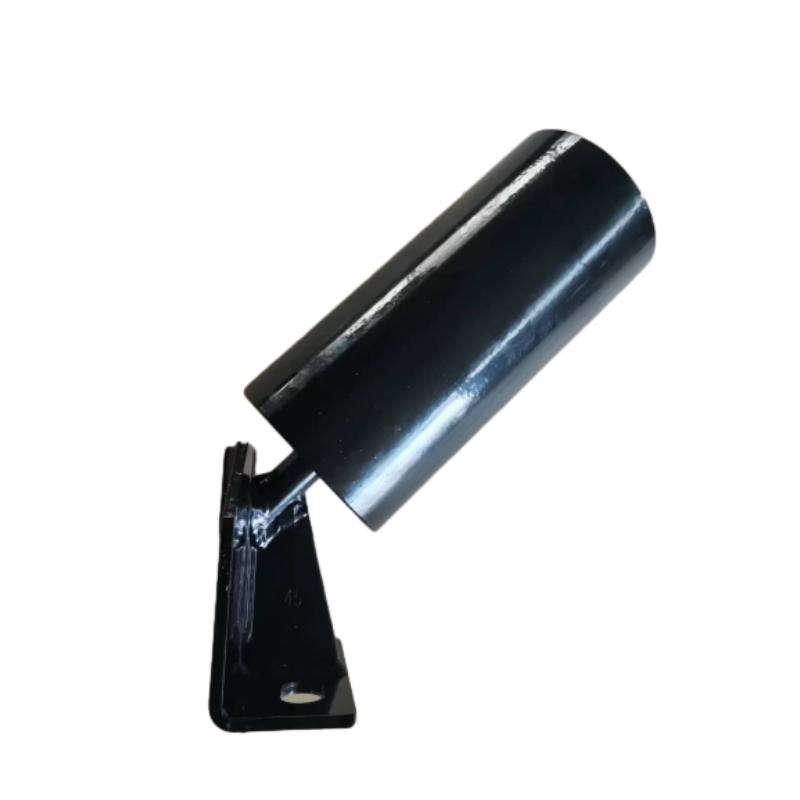
For environments where the conveyed material is particularly abrasive or corrosive, special types of idler rollers with protective coatings or materials are used
For environments where the conveyed material is particularly abrasive or corrosive, special types of idler rollers with protective coatings or materials are used
idler roller types. For example, rubber-covered idler rollers provide excellent resistance to chemicals and abrasion, making them ideal for use in chemical plants or wastewater treatment facilities.
In addition to their structural differences, idler rollers also vary in terms of their bearing types. Ball bearings are the most common type of bearing used in idler rollers due to their high load capacity and low friction. However, other types of bearings, such as roller bearings or needle bearings, may be used depending on the specific requirements of the application.
The versatility of idler rollers allows them to be customized to meet the unique needs of various industries. For instance, idler rollers with adjustable axles can be used to accommodate changes in belt tension, while those with special coatings can withstand extreme temperatures or harsh chemicals.
In conclusion, the evolution of idler rollers has been driven by the need for increased efficiency, durability, and adaptability in conveyor systems. From plain to flanged, rubber-covered to stainless steel, and ball to roller bearings, the variety of idler roller types available today reflects the ongoing innovation in this critical component of material handling equipment.