Belt Conveyor Idler Design A Comprehensive Guide
Belt conveyors are integral in a wide range of industries for transporting materials efficiently and cost-effectively. One critical component of these systems is the idler, which provides necessary support and guidance to the conveyor belt. In this article, we will delve into the design considerations of belt conveyor idlers, exploring their types, materials, and key features.
Types of Belt Conveyor Idlers
Idlers can be broadly classified into three categories return idlers, carrying idlers, and impact idlers. Return idlers are located at the end of the conveyor belt's journey and help in reversing the belt's direction. Carrying idlers, as the name suggests, support the weight of the material being transported and ensure its smooth passage over the conveyor. Impact idlers are designed to withstand harsh conditions, such as impact or heavy loads, and are often used in areas prone to spillage or jamming.
Material Selection for Belt Conveyor Idlers
The material selection for belt conveyor idlers depends on various factors, including the type of material being transported, the environmental conditions, and the specific requirements of the application. Common materials used for idler construction include high-strength steel, cast iron, and aluminum alloys. High-strength steel is known for its durability and resistance to corrosion, making it a popular choice for harsh environments. Cast iron is another popular material due to its good wear resistance and lower cost compared to high-strength steel. Aluminum alloys offer lightweight solutions while still providing adequate strength and corrosion resistance.
Key Features of Belt Conveyor Idlers
When designing belt conveyor idlers, several key features must be considered to ensure optimal performance and longevity. These include
1. Bearing type The bearing system plays a crucial role in idler performance. Ball bearings are commonly used due to their low friction and long life, while roller bearings are preferred for applications with higher loads Ball bearings are commonly used due to their low friction and long life, while roller bearings are preferred for applications with higher loads
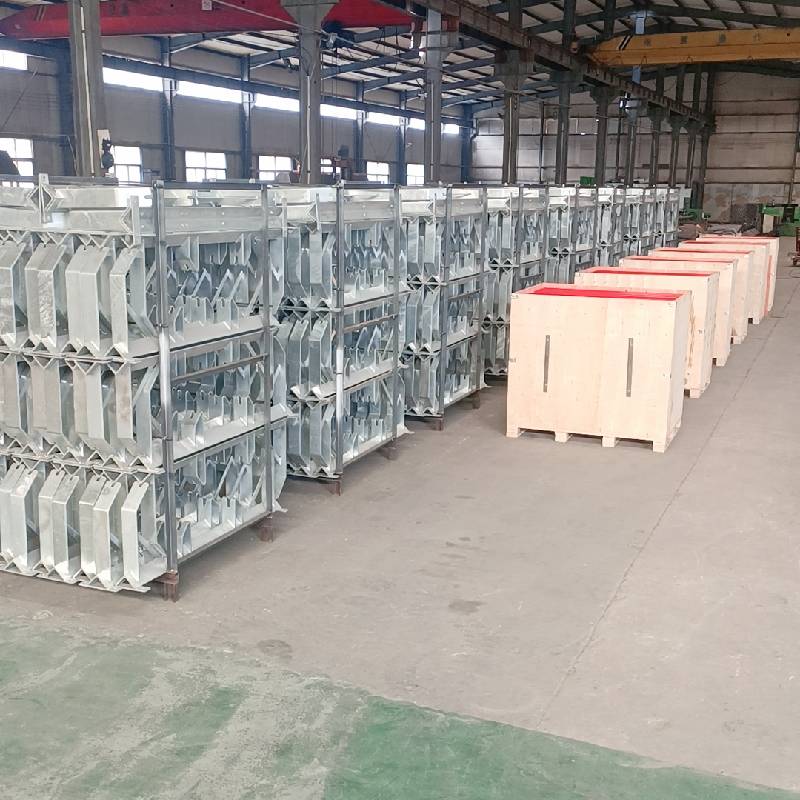
Ball bearings are commonly used due to their low friction and long life, while roller bearings are preferred for applications with higher loads Ball bearings are commonly used due to their low friction and long life, while roller bearings are preferred for applications with higher loads
belt conveyor idler design.
2. Frame design The frame must be sturdy and capable of supporting the idler and the weight of the conveyor belt and material. It should also be designed to withstand vibrations and other dynamic forces.
3. Alignment Proper alignment of idlers is essential to prevent belt misalignment, which can lead to premature wear and damage. Idler frames should be adjustable to accommodate variations in belt tension and alignment.
4. Wear resistance The idler components, especially the rollers and bearings, must be designed to withstand the abrasive nature of many materials being transported. Materials such as。
5. Corrosion resistance In harsh environments, idlers must be designed to resist corrosion. This can be achieved through the use of stainless steel or other corrosion-resistant materials.
In conclusion, belt conveyor idler design is a complex process that requires careful consideration of various factors. By selecting the right type of idler, material, and features, operators can ensure the efficient and reliable operation of their conveyor systems.