Navigating the world of conveyor pulley specifications can be a daunting task, especially when striving for efficiency and accuracy in industrial applications. Understanding the various aspects of conveyor pulleys is crucial for engineers and decision-makers seeking to optimize their production lines. This article delves into the practical and technical considerations essential for selecting the right conveyor pulley, underscoring the importance of experience, expertise, authority, and trustworthiness.
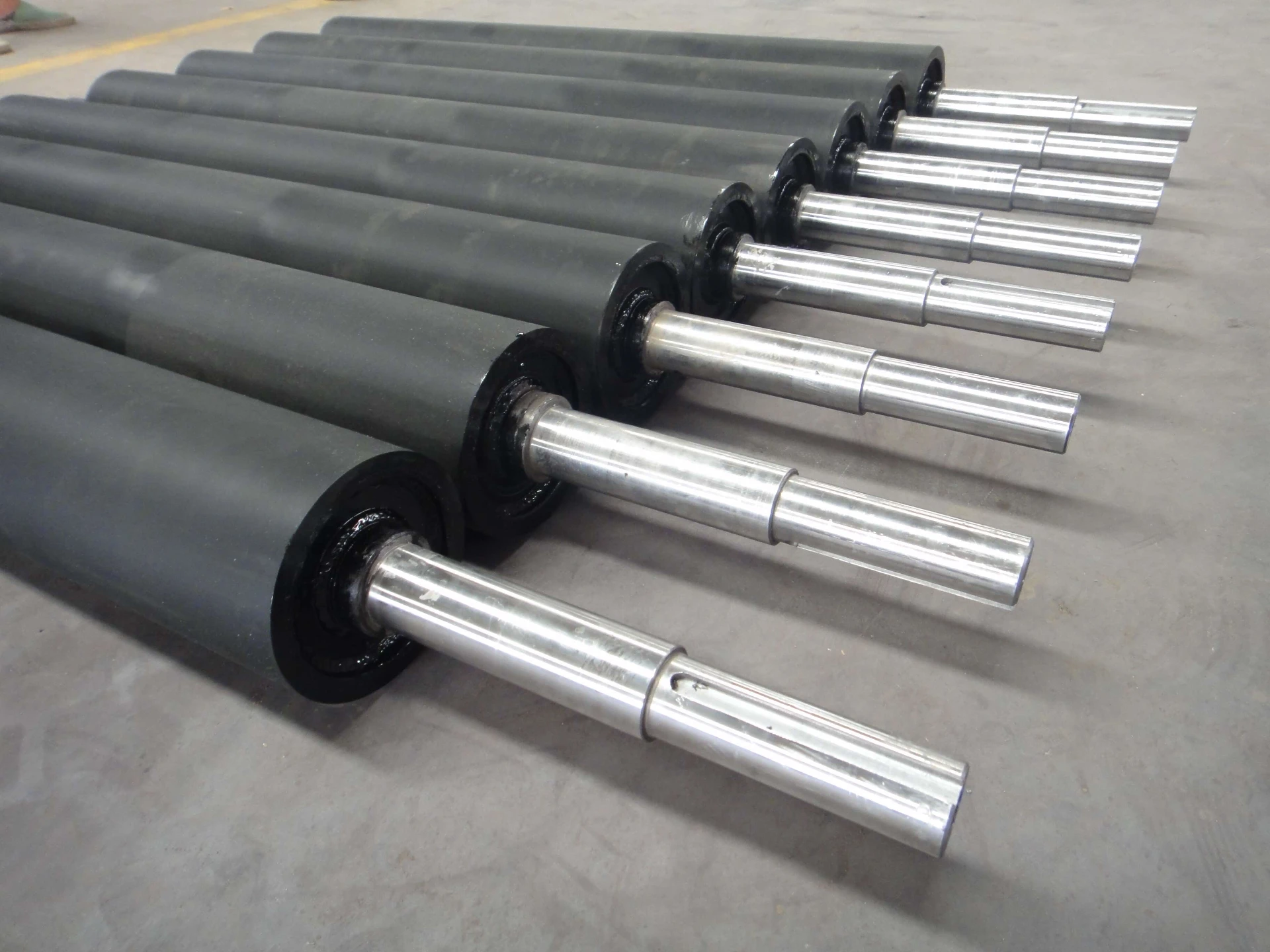
One of the primary considerations in conveyor pulley specification is the diameter and width of the pulley. These dimensions should align with the conveyor belt’s width and the load’s weight, ensuring optimal performance and longevity. A pulley that is too small can cause excessive belt tension and potential system failure, while an oversized pulley may inflate the initial investment without any real benefit. Veteran engineers have long recognized that balancing the diameter with the load size and type is essential for maintaining operational efficiency and reducing wear and tear.
Material selection is another critical factor that influences pulley specification. Steel remains the most commonly used material due to its durability and strength, particularly in heavy-duty applications. However, advancements in materials science have introduced alternatives like aluminum and composite materials, which are lighter and may offer sufficient strength in specific scenarios. Experienced professionals stress the importance of considering environmental factors such as humidity, temperature, and chemical exposure, as these can affect material integrity over time.
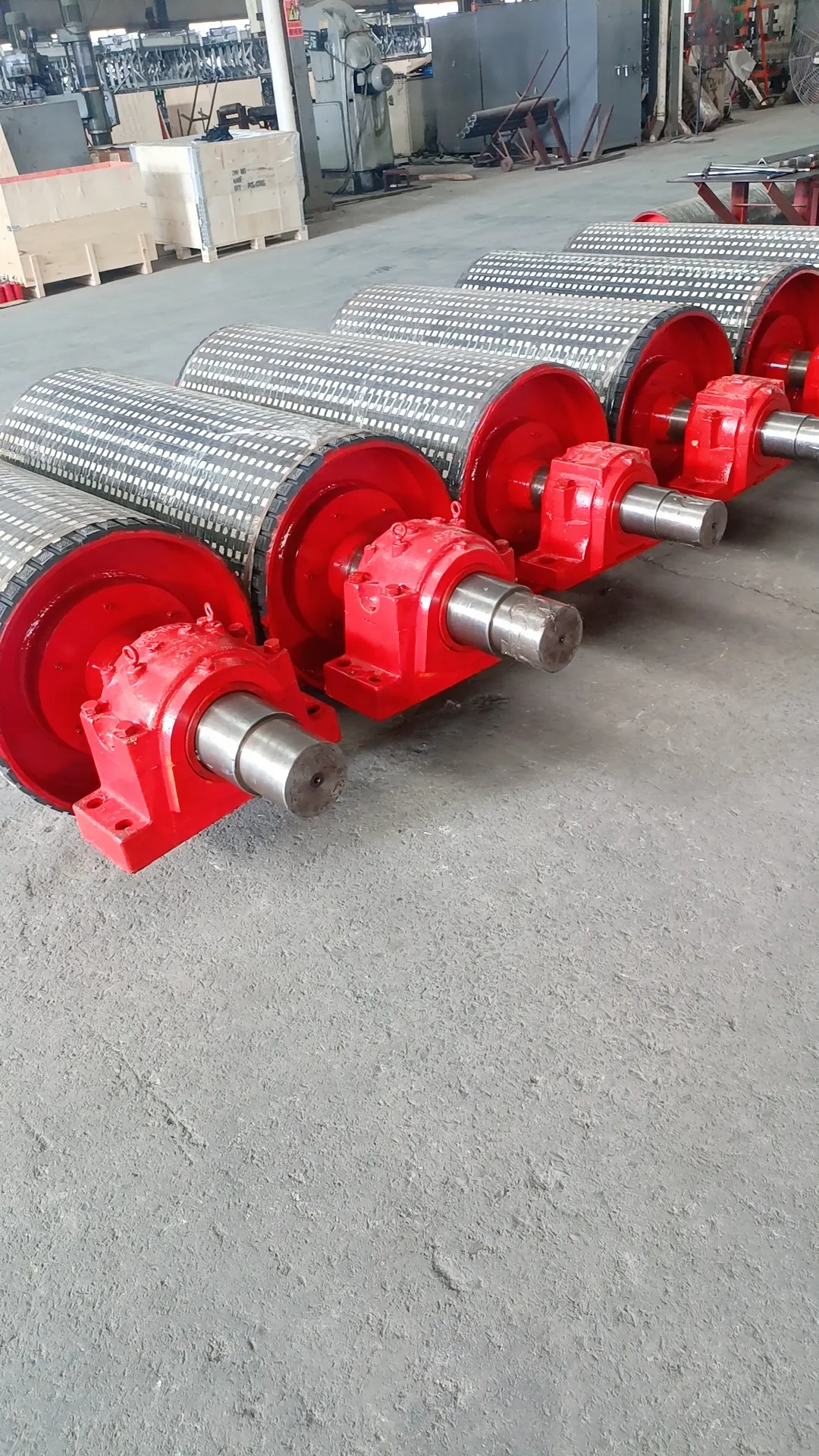
The type of pulley lagging is also a significant consideration. Rubber and ceramic lagging are popular choices, each providing distinct advantages. Rubber lagging offers excellent grip and shock absorption, making it suitable for general applications. Ceramic lagging, while more expensive, provides superior wear resistance and is often preferred in abrasive environments. Expertise in this area can guide the choice of lagging based on the operational conditions, dramatically enhancing the lifespan of the conveyor system.
conveyor pulley specification
To ensure efficiency, it's vital to pay attention to the bearing system used in the pulley. Bearings facilitate the rotation of the pulley, and their design can impact the system's performance. Roller bearings are commonly used due to their ability to handle radial loads, but for conveyors with high axial loads, ball bearings might be more appropriate. Experienced professionals often emphasize the importance of lubrication in maintaining bearing health, advocating for regular maintenance schedules to reduce friction and prevent premature failure.
Another specification to consider is the pulley’s shaft design, which must be robust enough to handle the load without deflection or bending. Shaft deflection can lead to misalignment, causing increased wear on both the pulley and the belt. By consulting industry standards and leveraging engineering calculations, manufacturers can design shafts that are optimized for both strength and weight, ensuring reliable and consistent conveyor operation.
Finally, surface finish and balance are subtle, yet vital components of pulley specifications. A smooth finish reduces friction and extends belt life, while proper balance prevents vibration, which can lead to mechanical failures over time. Industry authorities typically recommend precision balancing techniques during manufacturing to enhance overall system stability and efficiency.
In conclusion, selecting the right conveyor pulley involves a multi-faceted approach that considers dimension, material, lagging, bearing systems, shaft design, and finishing touches. By harnessing the collective wisdom of industry veterans and adhering to proven engineering principles, businesses can ensure their conveyor systems operate efficiently and reliably, minimizing downtime and maximizing productivity. Emphasizing these core elements in your conveyor pulley selection process not only underscores a commitment to quality but also reinforces a reputation built on expertise and trustworthiness in industrial applications.