In the engineering and manufacturing realms, the intricacies of conveyor belt idler design hold a pivotal role. Understanding the complex dynamics at play can significantly enhance operational efficiency and prolong the lifespan of conveyor systems, minimizing downtime and maintenance costs.
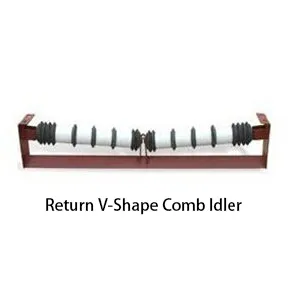
Fundamentally, a well-engineered conveyor belt idler functions as the supporting rotor that maintains the belt’s structural integrity during circulation. It is crucial to delve into the core components and considerations involved to grasp the full scope of its design.
First, identifying the specific requirements and constraints of the facility whether they relate to the transportation of goods through a factory floor or across vast mining landscapes is essential. Each environment demands tailored solutions; the one-size-fits-all approach could be a costly oversight. For instance, different materials require varied handling approaches, and the durability of idlers must match the abrasiveness and weight of the products being transported.
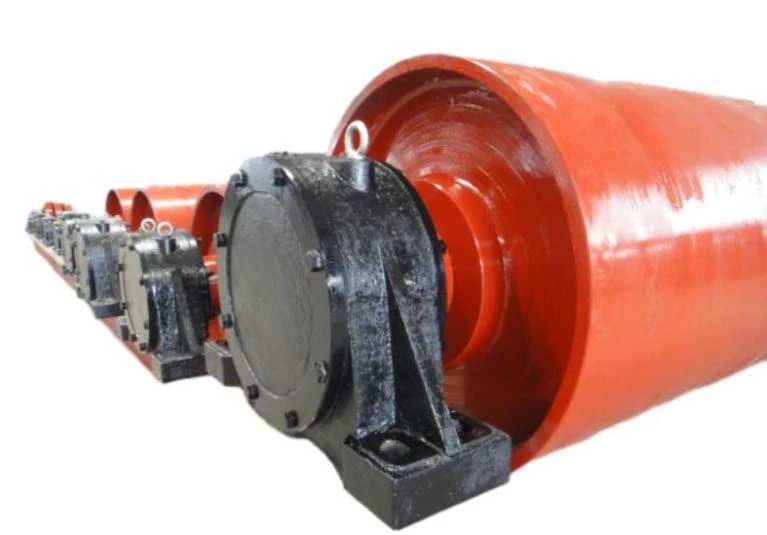
Material choice is another critical factor. Idlers crafted from robust materials like high-density polyethylene (HDPE) or steel are often ideal for reducing rotational inertia and lowering energy consumption. In industries like mining, corrosion resistance and anti-seize properties are critical, thus favoring specific alloys or composite materials. These materials not only sustain the mechanical impact but also resist harsh environmental conditions.
From an engineering perspective, precision in the balancing of the idler is paramount. Imbalance can lead to accelerated wear, noise pollution, and increased vibration, which, in turn, contribute to premature system failure. State-of-the-art balancing techniques can be employed during the manufacturing process to ensure optimal performance. Technologies like laser alignment and computational modeling can predict and rectify imbalance issues, securing smoother operation and enhancing the conveyor's operational reliability.
conveyor belt idler design
Additionally, the design consideration of bearing housing cannot be overlooked. Bearings must be adequately sealed to prevent contamination from dust, moisture, and other environmental factors prevalent in industrial settings. Thus, an efficient sealing system, potentially involving labyrinth or lip seals, ensures longevity by reducing maintenance intervals and preventing unexpected breakdowns.
Integration of modern monitoring systems is also a viable advancement. Smart idlers embedded with sensors and connected to a central monitoring system can provide real-time data analytics. These systems enable predictive maintenance by notifying operators of potential issues before they escalate into logistical bottlenecks, thus fostering a proactive maintenance culture.
Moreover, adherence to industry standards like the CEMA (Conveyor Equipment Manufacturers Association) guidelines is indispensable to ensure safety, interoperability, and optimal performance. These standards guide designers to maintain consistency and quality control throughout the idler production process.
In conclusion, pursuing excellence in conveyor belt idler design necessitates a thorough understanding of the application's specific requirements, an acute focus on materials and balancing, advanced bearing protection systems, and embracing technology for sustainability and durability. By adhering to these principles and engaging with authoritative industry standards, businesses can optimize their conveyor systems, ensuring efficiency, reliability, and cost-effectiveness well into the future.