The efficient operation of conveyor systems is vital to the success of many industries, from mining and manufacturing to logistics and distribution. At the heart of these systems lies a crucial component known as the conveyor take up assembly. Understanding the intricacies and functionalities of this component can significantly enhance the performance and reliability of conveyor systems, contributing to the seamless movement of goods and materials.
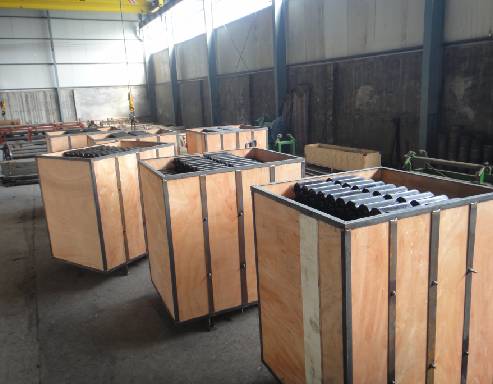
A conveyor take up assembly is designed to maintain appropriate tension on the conveyor belt throughout its operation. Proper tensioning is pivotal for preventing belt slippage, excessive wear, or system downtime. One of the primary functions of the take up assembly is to adjust for belt elongation and stretching caused by continuous usage and varying loads. Without a reliable take up assembly, the conveyor belt cannot operate at optimal efficiency, which can lead to costly operational disruptions.
In terms of design and application,
there are several types of conveyor take up assemblies. The gravity take up, for example, uses a counterweight to supply tension to the belt. This self-adjusting system efficiently accommodates changes in belt length and load. On the other hand, the screw take up requires manual adjustments via a threaded tensioning screw, offering precision but demanding regular maintenance checks. Lastly, the automatic or spring-loaded take up integrates sensors and actuators to sustain tension automatically, combining efficiency with reduced operator intervention.
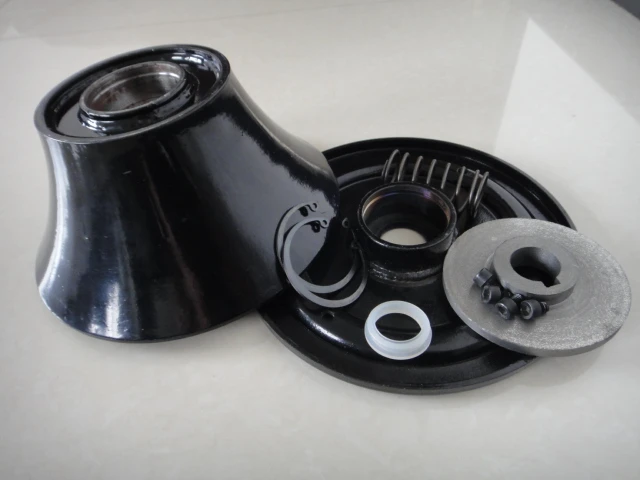
Experience within the industry has shown that choosing the right type of take up assembly depends heavily on the specific operational requirements and environmental conditions of the conveyor system. For instance, in environments with fluctuating temperatures or where significant belt length changes are expected, a gravity or automatic take up may be preferred due to their adaptability and reduced maintenance demands.
Professional expertise is fundamental in selecting, installing, and maintaining conveyor take up assemblies. Engineers and maintenance teams must evaluate factors such as the length and speed of the conveyor belt, load capacity, and environmental conditions before making a selection. Furthermore, regular monitoring and maintenance are imperative to ensuring the longevity and efficiency of the take up assembly. This includes routine inspections for wear and tear, realignment of parts, and timely replacements or recalibrations.
conveyor take up assembly
Authoritative sources in the field stress the importance of proper installation procedures. Incorrect installation can lead to inefficient performance, increased energy consumption, and premature equipment failure. Manufacturers and expert consultants can provide invaluable guidance, offering custom solutions tailored to specific operational needs, thus avoiding the pitfalls associated with generic, off-the-shelf components.
Trustworthiness in a conveyor system, enhanced by a well-maintained take up assembly, translates directly into reliability in operations. Businesses dependent on conveyor systems can ill afford the downtime associated with poorly maintained equipment. Real-world case studies have demonstrated that companies investing in high-quality conveyor take up assemblies experience fewer disruptions, lower maintenance costs, and improved overall productivity.
As technology continues to advance, innovations in conveyor take up systems are emerging. These include smart systems capable of real-time monitoring and adjustment, enhancing both the safety and efficiency of operations. For businesses seeking to stay competitive, embracing such technological advancements can provide a significant edge, ensuring that their conveyor systems are not only meeting current demands but are prepared for future challenges.
In conclusion, a conveyor take up assembly is a pivotal component in any conveyor system, ensuring optimal performance and longevity. By leveraging professional expertise to select and maintain the right type of assembly, businesses can achieve greater efficiency, reduce downtime, and maintain a competitive advantage in their respective industries. As industry practices evolve, staying informed about technological innovations in conveyor systems will be key to maintaining operational excellence and sustainability.