Pulley lagging is a crucial aspect in the world of conveyor systems, providing essential friction between the conveyor belt and the pulleys. This friction is vital in preventing belt slip and ensuring efficient power transmission. Understanding the different types of pulley lagging available can significantly enhance conveyor performance and longevity.
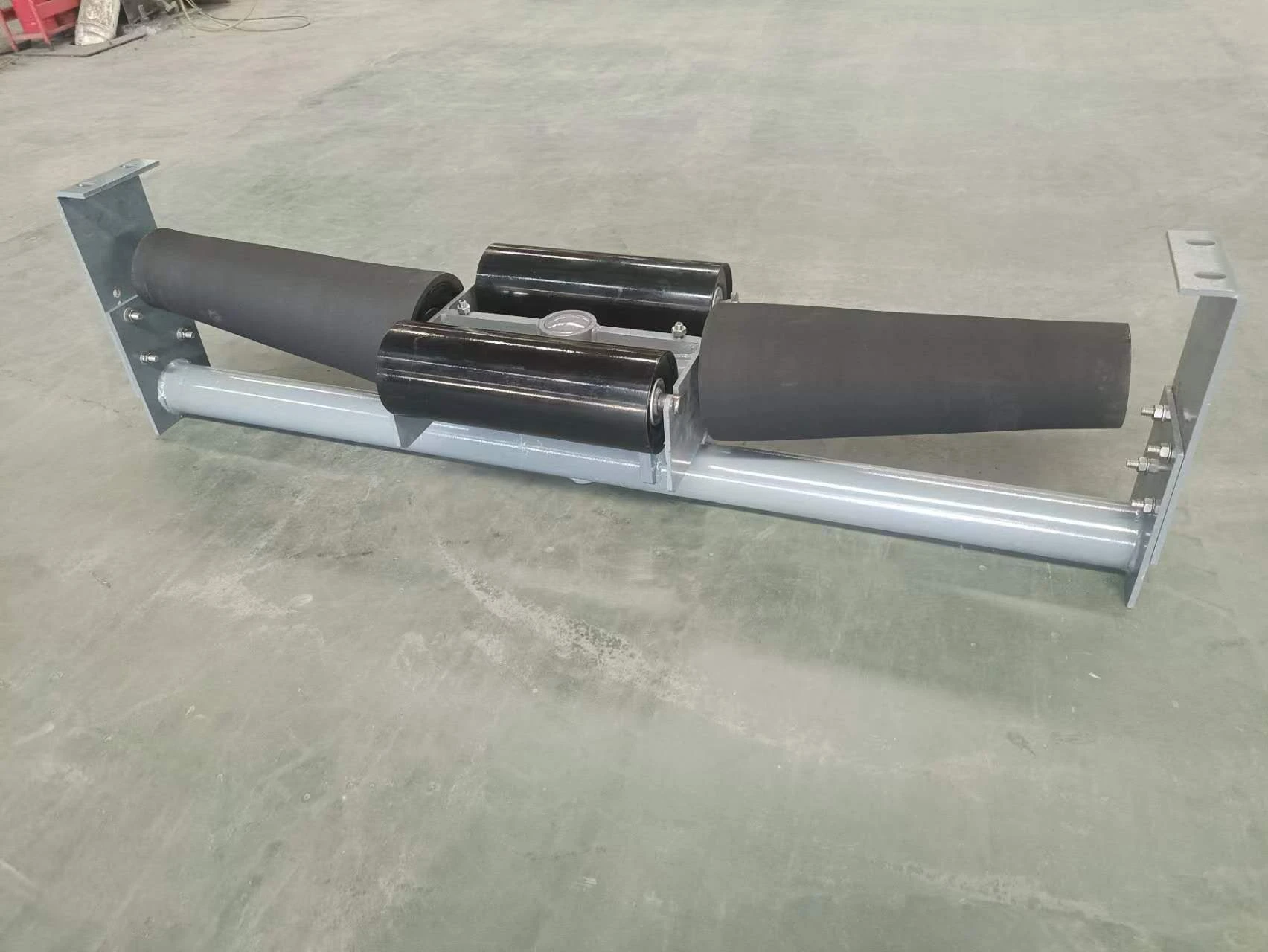
1. Rubber Lagging
Rubber, the most common type of lagging, is widely favored for its versatility and reliability. Rubber lagging offers excellent grip and cushioning and can be applied in different patterns such as plain, diamond, or herringbone. Its material properties make it ideal for general-purpose applications and environments with moderate wear and tear conditions. It's also cost-effective, making it the first choice for a range of industries. Moreover, rubber lagging is easy to replace, ensuring downtime is kept to a minimum.
2. Ceramic Lagging
For more demanding applications, ceramic lagging provides superior performance, especially with high-tension belt systems. Ceramic elements embedded in a rubber matrix offer enhanced wear resistance and increased grip. This makes it ideal for wet or muddy conditions, where slipping is a concern. However, the initial cost of ceramic lagging is higher compared to rubber. The trade-off is a prolonged life span and reduced maintenance frequency, making it a smart investment for operations where belt slippage is a persistent problem.
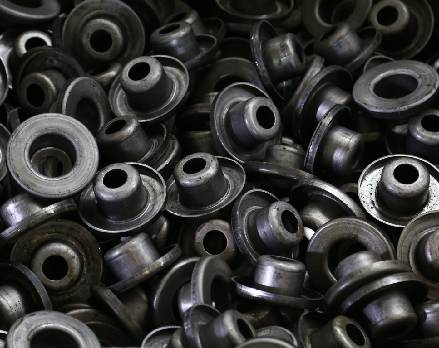
3. Polyurethane Lagging
Polyurethane stands out for its exceptional resistance to abrasion and impact, making it suitable for environments dealing with abrasive materials. Its flexibility and resilience also allow it to absorb shock loads effectively. Polyurethane lagging strikes a balance between rubber and ceramic by providing reasonable durability and grip, while maintaining a lighter weight. It's particularly beneficial in industries such as mining, where rock and aggregate are present.
4. Metal Lagging
Although not as common in modern applications, metal lagging might still be used in specific heavy-duty environments due to its robustness. Typically fabricated from steel, this type of lagging can withstand extreme conditions including high temperatures and heavy loads. However, metal lagging can increase the wear on conveyor belts and thus requires careful consideration.
types of pulley lagging
5. Specialty Lagging
For unique environments, specialty lagging such as flame retardant or anti-static variants are used. These offer targeted solutions—flame retardant lagging can be crucial for safety in industries prone to fire hazards, while anti-static lagging prevents build-up of static electricity in areas sensitive to sparks or explosions.
In choosing the right type of pulley lagging, several factors must be considered. The nature of the materials being conveyed, environmental conditions, operational temperatures, and budget constraints all play a role. Evaluating these will determine whether rubber, ceramic, polyurethane, or a specialty lagging is best suited for the task.
Expertise and authoritative guidance are essential in deciding the appropriate pulley lagging for your conveyor system. Consulting with industry specialists and reviewing case studies from similar installations will provide practical insights and trustworthiness in your final selection. This ensures not only optimal functionality and lifespan of your conveyor system, but also positions your operation to handle future challenges with confidence.
Each type of lagging has distinct advantages and potential drawbacks. By leveraging experience and expertise, and focusing on your specific operational demands, you can enhance both the efficiency and reliability of your conveyor systems, solidifying an authoritative edge over the competition in your industry.