Conveyor idlers are integral components in the world of material handling and are essential for the smooth and efficient operation of conveyor systems. Understanding the specifications of conveyor idlers is crucial for selecting the right product to meet your operation's needs. This article delves deep into the realm of conveyor idler specifications, drawing from real-world experiences, professional insights, and authoritative sources, ensuring you make informed decisions and enhance your system's performance.
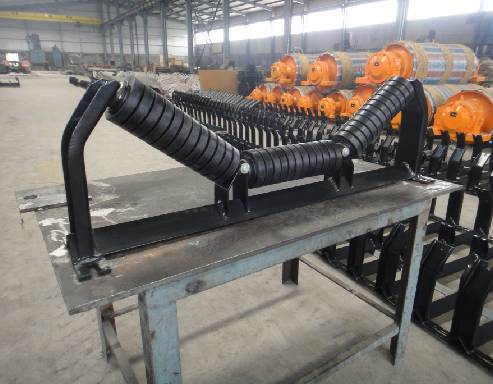
The role of conveyor idlers cannot be overstated—they support the conveyor belt and the material on it, facilitating a seamless transportation process across various industries. Their specifications dictate the efficiency and longevity of the conveyor system, and thus, require careful consideration.
1.
Diameter and Length The diameter and length of idlers are foundational specifications. Typically, larger diameters can handle heavier loads and are more durable, while smaller diameters are suitable for lightweight applications. Length, on the other hand, must correspond with the width of the conveyor belt, ensuring uniform support and reducing the potential for belt sagging.
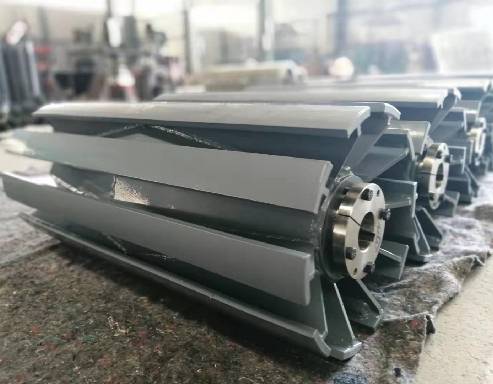
2. Material Composition Idlers are generally composed of steel or high-impact polymer. Steel idlers offer robust support and are ideal for heavy-duty operations. However, polymer idlers are gaining popularity due to their corrosion resistance and lightweight nature, which translates to lower power consumption and less wear on conveyor belts.
3. Sealing Design The sealing mechanism is often overlooked but plays a pivotal role in idler longevity. Effective sealing prevents dust, dirt, and moisture from infiltrating the bearing, which can lead to premature failure. Hermetic seals are especially recommended for environments plagued by particulates or extreme weather conditions.
4. Bearing Style Bearing specifications influence the idler's load capacity and rotational efficiency. Deep groove ball bearings come highly recommended for their ability to handle both radial and axial loads, which is essential in maintaining smooth rotation and reducing wear over time.
conveyor idler specifications
5. Shell Thickness The thickness of the idler shell directly impacts its durability. A thick shell is more resistant to deformation and wear, extending the life of the idler. It's advisable to select a thickness that matches the demands of your specific application.
6. Troughing Angle This specification is critical for load control and stability. Common angles range from 20° to 45°, with increased angles providing better support for bulkier materials, thus minimizing spillage.
7. Environmental Suitability Depending on operational settings, idlers must withstand various environmental challenges, such as temperature extremes, humidity, or aggressive chemicals. Stainless steel or specially coated idlers are recommended for corrosive environments, ensuring reliability and safety.
8. Load Capacity and Operational Speed Always align the idler's load capacity with the system’s operational requirements. Exceeding the specified capacity can result in mechanical failure. Additionally, synchronization with the system's speed ensures optimal performance and extends the life of both the idler and belt.
Having discussed these crucial specifications, real-world application and maintenance also play a significant role. Regular inspections and maintenance are advised to promptly identify wear and tear, especially in high-stress areas. Real experiences indicate that predictive maintenance can drastically reduce downtime and extend the lifespan of conveyor systems.
In conclusion, selecting an appropriate conveyor idler is a decision that marries technical specifications with realistic application insights. It's this blend of expertise, authoritative understanding, and trustworthiness in handling material that establishes a system's efficiency and reliability. By focusing on these specifications, industries can enhance productivity, reduce operational costs, and safeguard against unforeseen failures, ensuring seamless operations across their conveyor networks.