Conveyor pulleys play a pivotal role in the efficiency and efficiency of material handling operations across various industries. Understanding the nuances of selecting the right conveyor pulley for a specific application can greatly enhance operational efficiency and equipment longevity. This comprehensive guidance, rooted in extensive expert knowledge and hands-on experience, offers a valuable resource for optimizing conveyor systems.
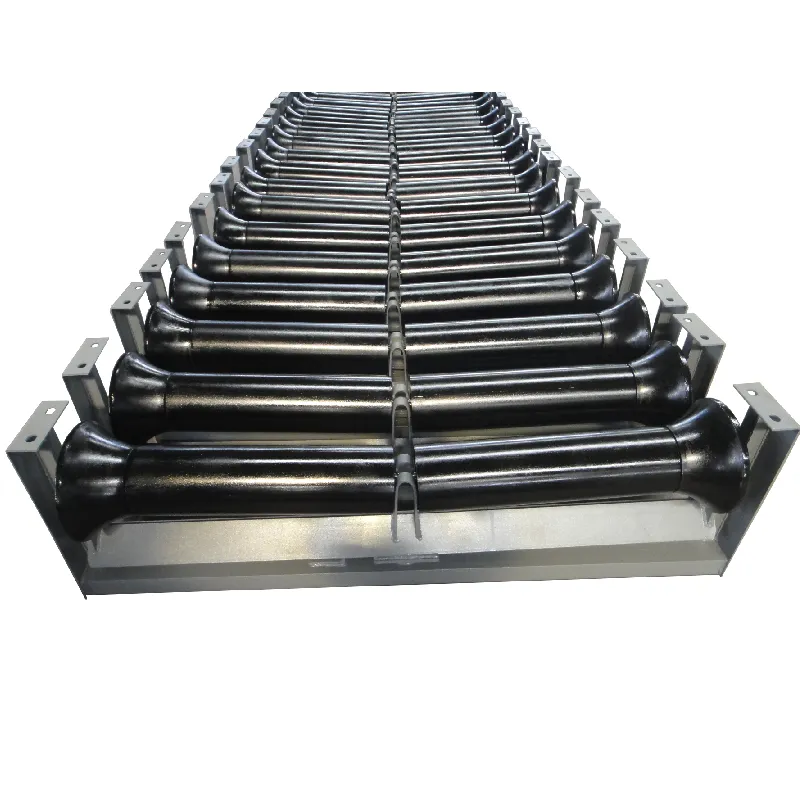
The selection of conveyor pulleys is a decision that encompasses several critical factors, each impacting the operation's performance. Firstly,
it is essential to consider the type of pulley. Drive pulleys, tail pulleys, and bend pulleys each serve unique functions and are selected based on the specifics of the conveyor system design. Drive pulleys, responsible for transferring the motor's power, need materials and surface coatings that ensure maximum friction and wear resistance.
Material selection plays a monumental role in the durability and performance of conveyor pulleys. Common materials include steel, stainless steel, and aluminum, chosen based on the environment in which the conveyor operates. Environments with high humidity or corrosive elements might necessitate stainless steel for its anti-corrosive properties. The surface finish of the pulley also warrants attention; rubber lagging, for instance, increases grip and belt protection, vital in heavy-duty applications.
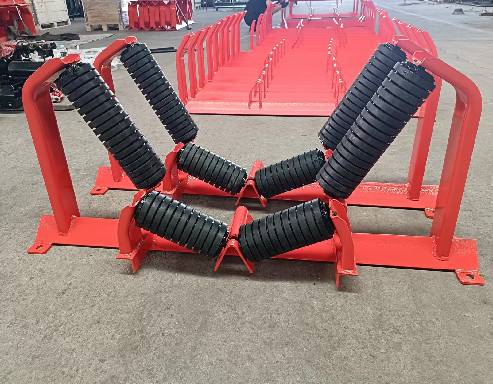
Bearing type and arrangement are other crucial elements determined by the operational speed and load. Precision-engineered bearings can vastly extend the life of a pulley and conveyor belt by minimizing friction and wear. Moreover, for operations demanding high reliability and uptime, selecting bearings with advanced sealing and lubrication systems can prevent particulate ingress and reduce maintenance needs.
conveyor pulley catalogue
Moreover, a key consideration is the pulley’s diameter, which significantly influences the belt’s tension and tracking, ultimately affecting product handling efficiency and system longevity. A larger diameter reduces belt stress, whereas too small a diameter might increase wear. Expert guidance often suggests calculating the correct balance of diameter and belt width for optimal performance.
Installation and maintenance are areas where expertise is indispensable for ensuring system performance. Proper alignment during installation minimizes belt slippage and uneven wear, paving the way for smooth operation. Implementing a scheduled maintenance regime, ideally based on operational data analytics, can predict wear patterns and prompt interventions before failures occur.
Decades of insights underscore the importance of understanding specific operational needs when consulting conveyor pulley catalogues. The perfect pulley is not an off-the-shelf purchase but rather the result of precise engineering aligned with unique operational parameters. By prioritizing customization and leveraging expert insights during the selection process, businesses can significantly enhance productivity, minimize downtime, and extend the functional lifespan of their conveyor systems.
In this rapidly evolving market, staying abreast of advancements in pulley technology can also confer competitive advantages, ensuring your material handling processes are not only effective but also cost-efficient. Aligning with reputable manufacturers who offer comprehensive technical support and manual resources will further bolster your position, ensuring your conveyor systems operate at peak performance with unparalleled trustworthiness and authoritativeness.