Conveyor pulley specifications are pivotal for efficient and reliable conveyor systems. As an integral component, the pulley influences both performance and longevity of the conveyor system. Understanding intricate details about its specifications can significantly enhance your operational efficacy and system management.
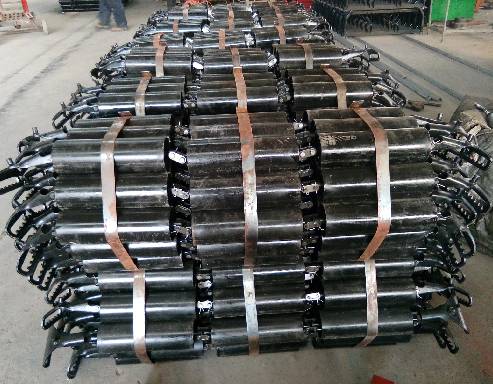
To begin with, acknowledging the basic types of conveyor pulleys is essential. The most prevalent categories include drive pulleys, tail pulleys, bend pulleys, and snub pulleys. Drive pulleys are the primary force application point in the conveyor, dictating the direction of the belt’s movement. Accurately choosing a drive pulley involves evaluating torque requirements, belt speed, and load weight, ensuring that the performance aligns with intended operational goals.
Precision in these specifications is key, and material selection is no exception. Conveyor pulleys can be crafted from several materials, each offering unique advantages. Steel remains a popular choice due to its durability and cost-effectiveness, yet aluminum and stainless steel are preferred for their weight advantages and corrosion resistance respectively. Specialized applications might also require pulleys coated with rubber or other materials to improve grip and reduce slippage.
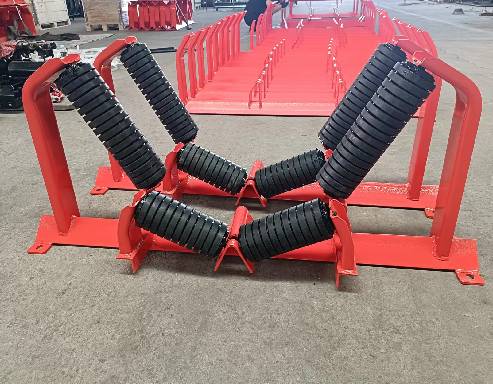
Diameter and face width are crucial technical specifications. The diameter must be chosen in accordance with the belt manufacturer’s guidelines, often proportionate to the belt's minimum operational bending radius, to prevent premature wear. The face width should be slightly wider than the belt to ensure stability and to prevent edge wear. Oversized pulleys can reduce the flexibility of the system and lead to material costs, whereas undersized pulleys may result in belt slippage and increased wear rates.
Another critical aspect is the construction of the pulley, which can be either welded or molded. Welded construction offers robustness for heavy-duty applications, while molded options provide lighter and more corrosion-resistant solutions for environments where these features are prioritized. Balancing these elements requires expertise and precision to augment both productive efficiency and mechanical resilience.
conveyor pulley specification
In terms of pulley coatings, lagging is an accessory that dramatically influences performance. Types of lagging such as rubber, ceramic, and polyurethane have different use-case scenarios. Rubber is commonly favored for general usage owing to its affordability and good friction attributes. Conversely, ceramic lagging is optimal for high-tension belts due to its superior grip and long-lasting properties, although it incurs higher initial expenses.
Operational environments further dictate the choice of pulley specifications. In abrasive conditions, enhanced wear resistance becomes paramount which may necessitate hardened surfaces or corrosion-resistant coatings. Where precision processing is significant, such as in food production or pharmaceuticals, stainless steel pulleys with high-grade finishes ensure compliance with stringent hygiene standards.
It’s worth noting that installation and maintenance regimes impact the long-term effectiveness of conveyor pulleys. Implementing regular check-ups and lubrication schedules ensures that components remain in good condition, mitigating the risks of unexpected downtimes and costly repairs.
In summary, a deep understanding of conveyor pulley specifications is instrumental in optimizing conveyor systems. Selecting the appropriate pulley involves a holistic view of operational demands, environmental conditions, and material durability. Investing in high-quality conveyor pulleys is not merely about meeting present demands but ensuring prolonged reliability and efficiency, thereby gaining a significant advantage in competitive industrial landscapes.