Conveyor systems have carved a niche in a multitude of industries, ensuring seamless transportation of materials and goods within facilities.
A critical component of these systems is the conveyor roller. Knowing the different types of conveyor rollers enhances operational efficiency and longevity. Here, we dive into the nuances of these rollers with insights grounded in extensive industry expertise and real-world applications.
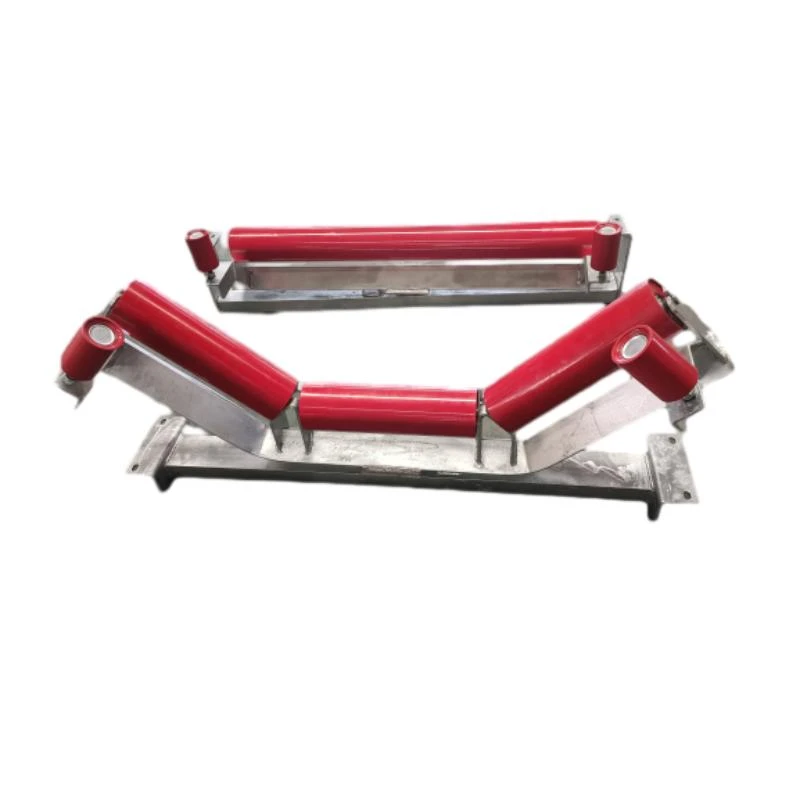
1. Gravity Rollers
Gravity rollers are pivotal in creating simple, cost-effective transport solutions. These rollers rely on the force of gravity for movement, which makes them ideal for horizontal or slightly inclined systems. Particularly common in assembly, packaging, and distribution sectors, gravity rollers require minimal maintenance due to the absence of power-driven components. Industries benefit from their straightforward installation and operational reliability, which can significantly streamline low-complexity material handling needs.
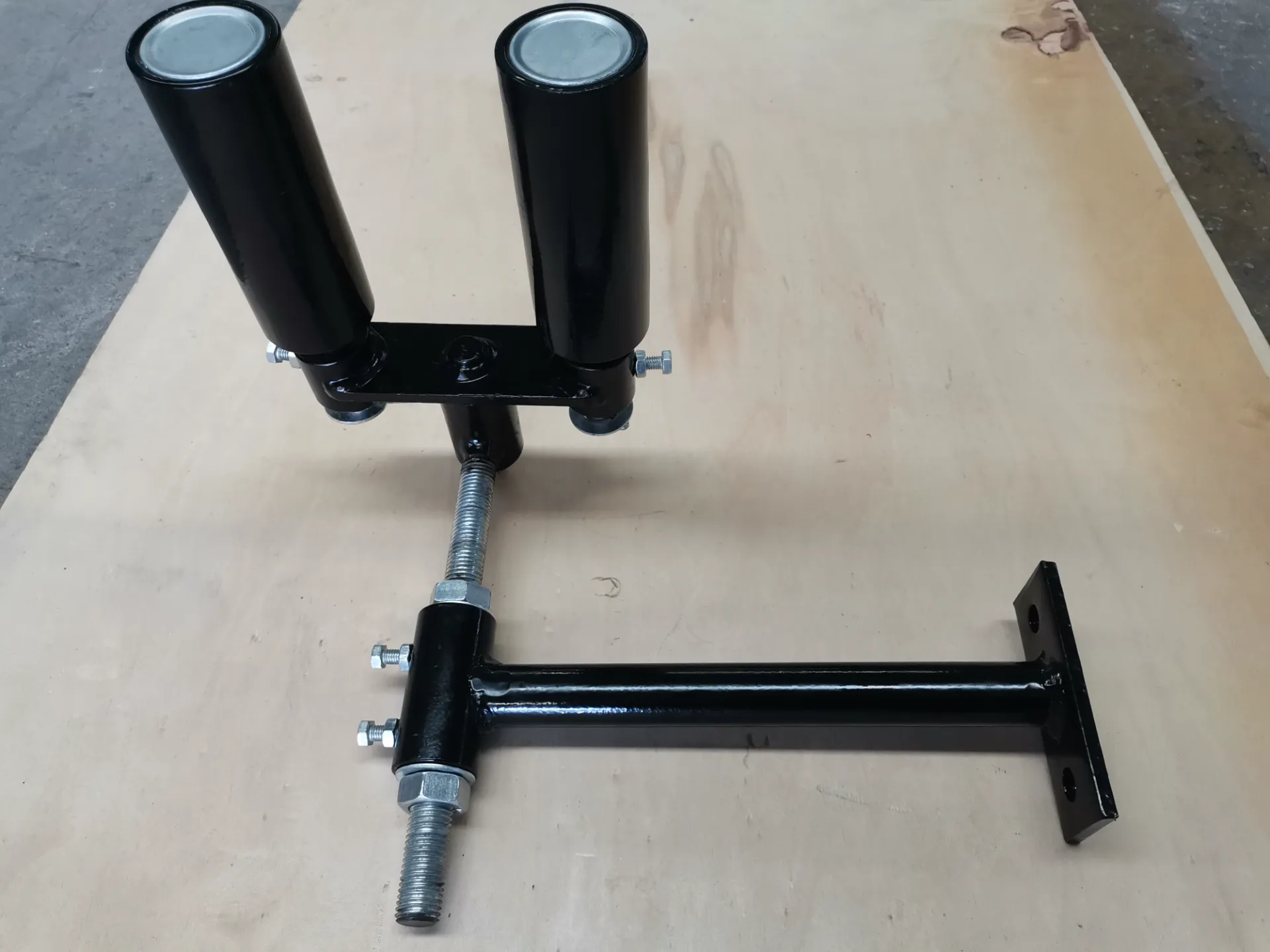
2. Chain-Driven Rollers
Chain-driven rollers are indispensable when handling heavy duty applications. Their robust construction supports heavy loads with precision and reliability. The integral chain system ensures synchronized movement across rollers, preventing mishaps common in high-load environments. These rollers are often found in automotive manufacturing and large-scale material transport. Their robust nature underscores the necessity for regular inspections and maintenance to sustain their long lifecycle and minimize operational downtimes, which is crucial in high-stakes industries.
3. Belt-Driven Rollers
Providing quiet and efficient operation, belt-driven rollers are the foundation of many conveyor systems. These rollers are pivotal for light to medium duty applications where speed and low noise are paramount. The automotive and food processing industries benefit immensely from their adaptable design, allowing for swift movement of products with minimal human intervention. Regular belt inspections and tension adjustments are vital in preserving their performance, which translates to consistent productivity and low energy consumption.
4. Accumulation Rollers
different types of conveyor rollers
Designed for controlled flow and buffering within conveyor systems, accumulation rollers are essential in managing production line pacing. They allow for accumulation without exerting pressure on conveyed items, reducing the risk of product damage. This feature is particularly beneficial in fragile goods transport, such as electronics and consumer goods. Conveyors in such settings demand precision, wherein careful calibration of speed and pressure can significantly enhance throughput and product protection.
5. Tapered Rollers
Optimized for use in curved conveyor sections, tapered rollers ensure uniform loading across curves, keeping products centrally aligned. Their design is critical for facilities with complex layouts requiring directional changes. The parcel and luggage handling industries heavily utilize tapered rollers for their efficiency in conserving space and maintaining product orientation through turns. Regular monitoring of alignment and wear plays a crucial role in sustaining their effectiveness in high-turnover environments.
6. Plastic and Stainless Steel Rollers
Material choice in rollers has profound implications on efficiency and suitability for specialized environments. Plastic rollers offer corrosion resistance and are ideal for light-duty and hygienic applications, especially in food processing and pharmaceuticals. Conversely, stainless steel rollers boast exceptional durability and resistance to harsh conditions, favored in chemical processing and outdoor environments. Understanding the operational environment guides selection, making it critical to weigh factors such as load capacity, speed, and environmental conditions.
7. Live Roller Conveyors
Live roller conveyors, powered by rollers, are adept at facilitating precise product movement and spacing. Their application is widespread in sorting and packaging sectors where accuracy and speed are paramount. They easily integrate with automated systems, driving higher efficiency and responsiveness. Ensuring proper lubrication and motor function is key to preventing breakdowns in high-velocity operations, maintaining a smooth flow that reduces bottlenecks and enhances supply chain agility.
In choosing the appropriate type of conveyor roller, facility managers must consider the specific needs such as load, speed, environmental factors, and maintenance capabilities. Leveraging expert insights, these decisions drive operational excellence. The right selection and upkeep of conveyor rollers not only mitigate risks but also align industrial operations with the evolving demands of technology-driven markets. This nuanced understanding validates the authority and trustworthiness of deploying the right roller type tailored to unique industrial needs, ensuring durability, efficiency, and optimized performance.