Conveyor pulley lagging material plays an essential role in the efficient and effective operation of conveyor systems, which are crucial in sectors such as mining, manufacturing, and logistics. Selecting the right lagging material not only enhances the longevity of the conveyor pulley but also significantly improves the system's overall performance. This article delves into various aspects of conveyor pulley lagging material, offering insights drawn from industry expertise and authoritative sources to aid you in making informed decisions.
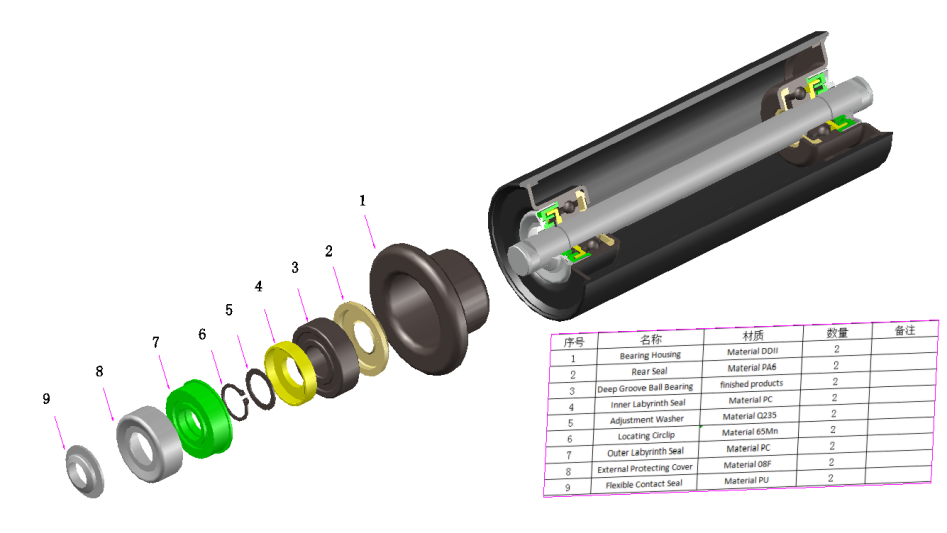
Conveyor systems are integral to many industrial operations, often running 24/7, and requiring minimal downtime to maintain productivity. One critical component in these systems is the conveyor pulley. Lagging, applied to the surface of the pulley, provides increased traction, reduces wear, and helps prevent belt slippage. The choice of lagging material should be aligned with the specific operational demands of your conveyor system.
Among commonly used materials, rubber lagging stands out for its versatility and cost-effectiveness. It offers good grip and cushioning, which protects both the pulley and the conveyor belt. Rubber is suitable for general-purpose use, particularly in industries where resistance to water and moderate levels of abrasion are needed. For applications demanding more robust performance, ceramic lagging provides superior resistance to wear and tear, coupled with excellent grip, minimizing slip and extending the lifespan of both the belt and the pulley.
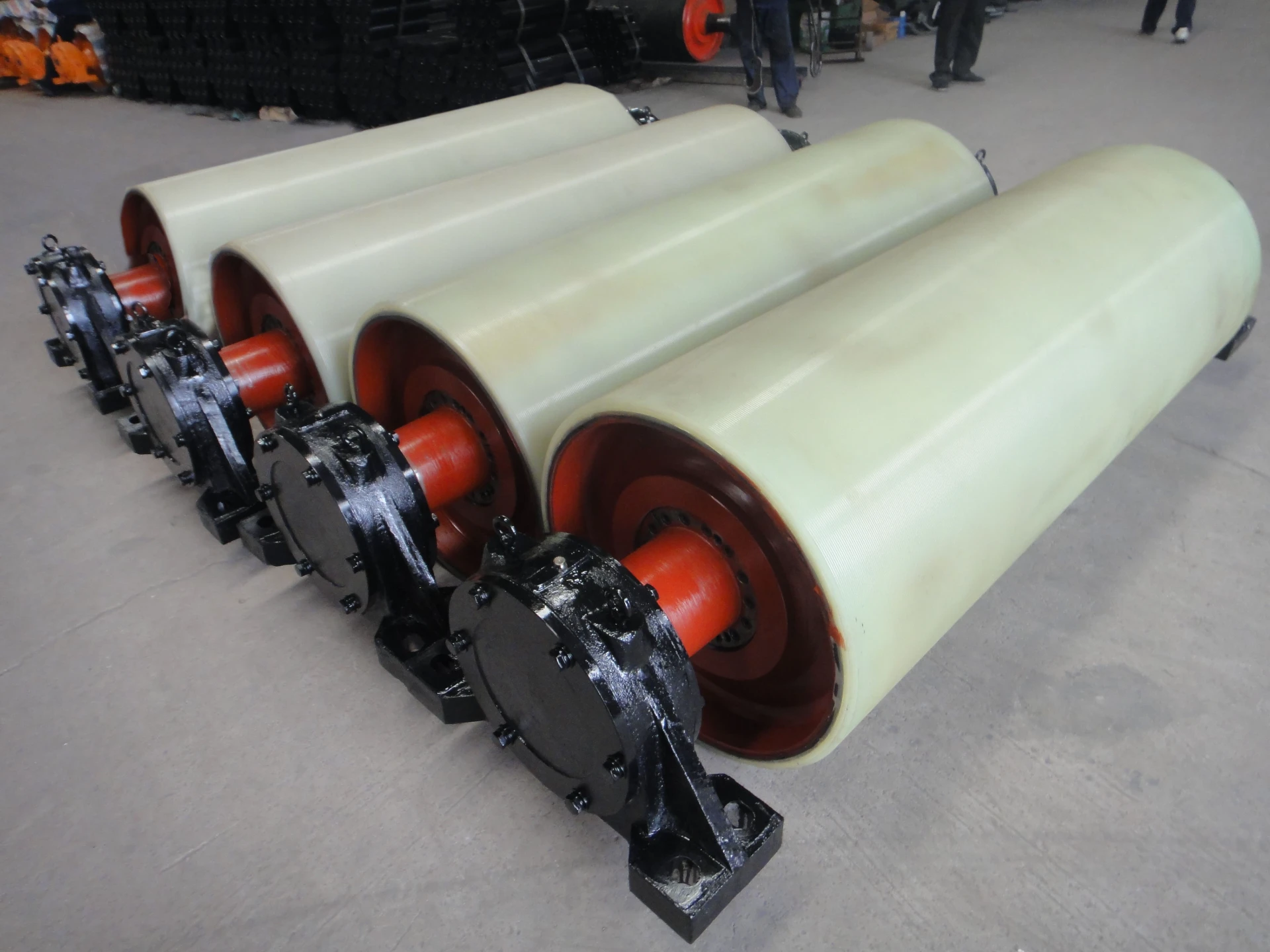
Polyurethane lagging is an excellent choice for high-tension environments. It delivers remarkable durability, resisting cuts and tears, which makes it ideal for heavy-duty operations such as in mining or bulk materials handling. Its resilience against chemical degradation further enhances its utility in environments where exposure to oils, solvents, or other corrosive substances is a concern.
For environments that experience high levels of corrosion or extreme temperatures, metal lagging offers a viable solution. While more expensive, metals such as stainless steel or zinc-coated steel provide unparalleled strength and weather resistance. These properties make metal lagging suitable for outdoor installations or in industries where hygiene and sterility are paramount, such as food processing.
conveyor pulley lagging material
In selecting the appropriate lagging material, it’s essential to consider not only the physical and environmental demands of the operation but also maintenance and operational costs. Properly installed and chosen lagging can dramatically reduce operational costs over time by minimizing downtime, maintenance, and energy consumption.
Compressor systems often require specifically tailored lagging solutions to enhance operational efficiency.
Installation precision is also key. Improperly fitted lagging can lead to uneven wear and tear, increased energy usage, and potential safety hazards. Therefore, seeking expertise from experienced professionals during installation can be a valuable investment.
When reviewing lagging solutions, it’s advisable to partner with a supplier or manufacturer with a solid reputation and proven track record. Look for industry-standard certifications and customer testimonials to gauge their reliability. A trustworthy supplier will not only provide quality materials but also offer valuable advice and support in choosing and maintaining the right lagging solution for your specific needs.
In conclusion, the importance of selecting the appropriate conveyor pulley lagging material cannot be overstressed. It directly impacts the efficiency and longevity of your conveyor system. By understanding the demands of your operational environment and the properties of various lagging materials, you can make an informed decision that enhances productivity and safeguards your investment. With expert advice and reliable materials, you can ensure that your conveyor system operates smoothly and efficiently, contributing to your business's overall success.