Pulley Lagging An In-Depth Analysis of Types and Applications
In the realm of mechanical engineering, pulleys play a pivotal role in transmitting power and force through various systems, particularly in lifting mechanisms and belt drives. However, a common issue that arises with pulleys is lagging, which can significantly affect their efficiency and longevity. Understanding the different types of pulley lagging is crucial for optimizing machinery performance and ensuring optimal maintenance. This article delves into the key types of pulley lagging and their implications.
Firstly, let's define what pulley lagging is. It refers to the separation or slipping between the pulley's surface and the belt that runs over it. This phenomenon occurs due to factors such as frictional wear, heat, and material degradation. To combat this, engineers employ lagging materials that provide a protective layer and improve the grip between the pulley and belt.
1. Rubber Lagging Perhaps the most popular type, rubber lagging is made from vulcanized rubber, offering excellent friction and resistance to wear. It is lightweight, flexible, and easy to install, making it ideal for low-speed applications. However, it may degrade over time and is less suitable for high-temperature environments.
2. Neoprene Lagging A synthetic alternative, neoprene lagging offers better heat resistance than rubber, making it an excellent choice for industrial machinery exposed to elevated temperatures. It also provides good abrasion resistance, but its flexibility is somewhat less than rubber.
3
3
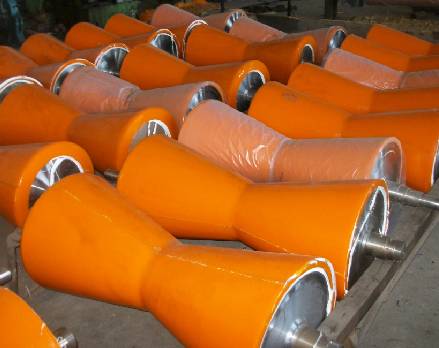
3
3
pulley lagging types. Fiber Reinforced Lagging Comprised of a blend of fibers like asbestos, fiberglass, or Kevlar, fiber-reinforced lagging provides exceptional strength and durability. It withstands extreme temperatures and high-speed operations, making it ideal for heavy-duty machinery. However, asbestos-lagging is no longer used due to health concerns.
4. Synthetic Leather Lagging This modern option combines the benefits of leather-like grip with synthetic materials, providing a long-lasting solution resistant to moisture and chemicals. It is particularly useful in environments prone to corrosion.
5. Self-Lubricating Lagging Designed to minimize friction, self-lubricating lagging incorporates additives that create a film on the pulley surface, reducing wear and extending the life of the pulley. These materials are particularly beneficial in situations where oiling is challenging or not feasible.
Proper selection and application of pulley lagging types are essential to prevent excessive wear, reduce noise, and maintain system reliability. Regular inspections and timely replacement of lagging materials ensure that the machinery operates efficiently and safely.
In conclusion, understanding the various types of pulley lagging allows engineers to make informed decisions when designing or maintaining mechanical systems. Each type offers unique advantages and limitations, and choosing the right one depends on the specific application, operating conditions, and safety requirements. By addressing lagging effectively, engineers can optimize the performance and lifespan of pulley-driven machinery.