In the realm of industrial machinery and conveyor systems, the importance of drum pulley lagging cannot be overstated. As a crucial component, it can make the difference between optimal efficiency and frequent downtimes. By understanding its role, professionals across sectors can ensure they maximize their conveyor system’s performance and longevity.
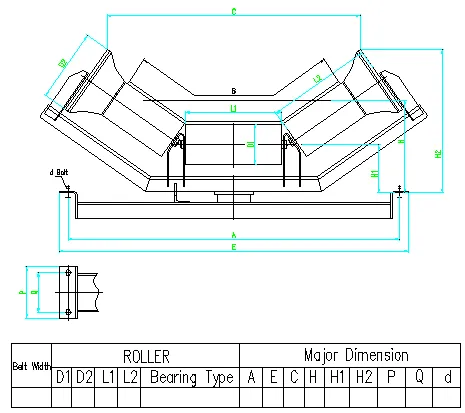
Drum pulley lagging, a technique involving the application of a coating or surface treatment to the driven pulley in conveyance systems, offers multiple benefits. These include enhanced traction between the belt and pulley, improved resistance to wear and tear, and protection against material build-up. When done correctly, lagging can significantly reduce belt slippage, one of the leading causes of conveyor inefficiency.
From an experiential standpoint, industries that have employed high-quality drum pulley lagging report a notable decrease in maintenance costs and downtime. For example, in the mining sector, where abrasive materials are frequently transported, lagging has proven essential in extending the lifespan of the pulley by absorbing the energy from material impacts and reducing the friction that typically accelerates wear. This real-world application underscores the technique's practical benefits and contribution to sustainable operations.

Experts in materials science and mechanical engineering provide critical insights into the design and implementation of effective drum pulley lagging. The choice of material is paramount; rubber is commonly used because of its cushioning properties and resistance to abrasion, but ceramics offer superior durability in aggressive environments. Rubber, specifically with a diamond groove or herringbone pattern, enhances grip and channels away water or debris, improving the belt's contact with the pulley.
Ceramic lagging, although more costly, excels in environments exposed to high tension and heavy loads, providing unmatched resistance against harsh conditions. Expertise in selecting the right lagging material involves assessing various operational demands, such as the transported materials, environmental conditions, and system load requirements.
drum pulley lagging
Industry authority figures advocate for regular inspection and maintenance as part of a comprehensive lagging strategy. Over time, even the best lagging materials can degrade, leading to reduced effectiveness and potential system failures. Routine checks ensure that any signs of wear or damage are promptly addressed, maintaining system efficiency and performance. Trusted manufacturers and service providers often offer warranties and support to reassure clients of the durability and quality of their lagging solutions, adding an extra layer of reliability and credibility.
Furthermore, the trustworthiness of a supplier or service provider in the drum pulley lagging market is a crucial factor. Renowned companies often invest in ongoing research and development, ensuring their products embody the latest advancements in technology and materials. Clients are encouraged to verify certifications, client testimonials, and industry reputation before making a purchase, as these elements collectively build the trust required for long-term partnerships.
Integrating advanced technology with traditional lagging methods has paved the way for innovative products. Self-monitoring lagging systems are emerging, which can provide real-time data on wear patterns and operating efficiency. Such innovations ensure that businesses not only optimize their immediate operations but also predict and plan for future maintenance, ultimately reducing downtime and optimizing resource allocation.
For companies seeking a competitive edge via drum pulley lagging, understanding and leveraging these principles is crucial. By balancing practical experience, expert advice, and our evolving understanding of materials and technologies, businesses can ensure they select and maintain the most effective conveyor systems. The careful integration of trusted, authoritative practices into operational procedures is key to operational excellence and efficiency in conveyor system management. Through the strategic application of drum pulley lagging, organizations can safeguard their assets, enhance productivity, and maintain their competitive stance in dynamic markets.